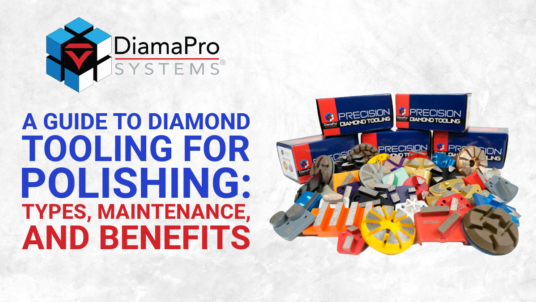
Buying tooling that has been manufactured under strict, quality controls is important. Having uniformity in the diamond tools will outperform a poor-quality, low-cost tool every day of the week. Tool performance equates to efficiency, which increases production and leads to greater profit. Having consistent, quality tooling will offer a greater opportunity for a consistent, repeatable result.
What Is Diamond Tooling and How Does It Work?
Industrial diamond tooling designed to be attached to a walk-behind concrete grinder is made up of three parts. The base, bonding material, and diamonds of varied sizes or grits. All three are produced in different configurations that allow you to select a tool according to the task and substrate.
When evaluating a concrete substrate, it will appear to be hard. Concrete has great compressive strength to withstand high loads. When selecting abrasive diamond tools to grind concrete, the compressive strength is a value that is important, but the surface hardness is what really needs to be found. You will be grinding only the surface so the load bearing capability (compressive strength) should not be of concern. You can have high compressive strength with a weak, friable surface.
The industrial diamond does the cutting. Diamonds are produced in different grits or sizes. The larger the diamond particle, the more aggressive it will be. The first step when polishing a slab will be considered the grinding phase. This phase will also be performed when preparing a surface when installing a resinous coating system. It provides the coating with a rough, clean surface to bond to.
Grinding is the first step when polishing a concrete surface. The second is to hone the surface. Honing will reduce the depth of the scratch produced when grinding by 50%. The next step is to polish. For example, when going from grinding to honing, the scratches will be reduced by 50% with each added step. Eventually, the scratches become invisible to the eye. At this point, the surface will have a high, medium, or low gloss depending on which diamond grit you stop at.
Types of Concrete Diamond Tooling
Every grinder is designed to hold diamond tooling. The attachment style will dictate the configuration of the tooling base being used. There are diverse ways that make the connection between the tool and the grinder plate or arm.
Now, the terminology to describe the attachment types will vary. Even if you don’t recognize the style name in this blog, describing the attachment style to your supplier will help them locate one that fits the grinder.
A slide-in mechanical attachment is extremely popular. It might be called a wing-back or trapezoid. Some trapezoids use screws to hold them in place and do not rely on a friction fit. The slide-in attachment allows you to easily slide the tool into the plate. There might also be a magnet in the center, adding extra security once fitted.
There are also Velcro back tools. These are typically less aggressive (higher grit) tools and do not need to have a high-strength attachment. Velcro backs are usually used during the honing and polishing phases.
Before the grinding tools can be selected, the hardness of the surface needs to be evaluated. This is critical to ensure long tool life with the highest production level. The surface hardness is found using the MOHS Hardness Test. This test will aid in selecting the grinding tool bond hardness.
The bond material is what encapsulates the diamond particles which are then adhered to the base. With grinding tools, the bonding material is a metal alloy. Metal alloy is strong, having the ability to hold onto the coarsest diamonds. Other bonding materials do not have the strength to perform when aggressive grinding is done.
When grinding, there needs to be exposed diamonds that do the cutting. As the diamond particles wear, new diamonds need to be exposed to continue with the process. As the diamonds wear, the bond material also needs to be worn. This will expose new abrasives. The bond material is produced in different hardnesses. The reason is that the bond hardness correlates to the hardness of the surface. This is where the MOHS Hardness value comes into play. If the surface tests at a lower value (soft) a hard bond should be used. If the hardness value is high (hard) a soft bond will work the best. If a soft bond is used on soft concrete, it will still cut but the tooling life will be shortened and will increase the cost of the project.
When honing concrete, diamonds are medium-sized. This size particle does not need to have a bond as strong as when grinding. Materials such as copper, ceramic, and hard resins are used effectively. Like metal bond tooling, as you grind the particles wear. As they wear, the bonding material also must be worn to expose fresh diamonds. Concrete hardness has a much less impact on this bond. The bond is considered medium hardness to work on most slabs.
Polishing tool diamonds are encased in a softer resin. These particles are exceedingly small. The resin will wear at a slow rate providing a long tooling life because the surface is already smooth.
The Importance of Diamond Tooling Maintenance
Visually inspecting the tooling as they are removed from the grinder is extremely important.
Uneven tool wear will negatively impact the final appearance of a polished floor. When one tool wears more than the others it could be due to a bent tool holder. No matter how often you change out the tools, this will keep repeating itself. Broken or poorly adjusted drive belts could also be the culprit. This has nothing to do with the quality of the tool, it is a mechanical issue that needs to be taken care of.
Maintenance of the tooling consists of visual inspection, keeping them clean and free of impacted cement dust, and storage. When dry polishing, the tools stay cleaner. There might be dust, compressed between the segments, but overall, minimum cleaning will be needed.
When wet polishing, cement slurry will be generated. After the tool has been removed from the machine, it is important to inspect each tool for wear and remove the impacted slurry. Placing them in a bucket of water will help before the slurry has dried. Do a final cleaning before they are put back into their boxes or holders. This will provide you with a long, lasting service life.
Benefits of Using High-Quality Diamond Tooling
Like all other manufactured products, tools might appear to be like another but once you start using them, they are worlds apart. The term quality, when speaking of diamond tooling, can mean different things. The quality of the base, bonding material, and diamond particles are all important.
The base is a cast or machined part designed to fit into a complimentary holder. Ithe f casting method is poor or the metal composition is subpar, the tool will not remain fixed to the grinder during aggressive cutting. Having tools come loose and fly across the floor can be dangerous.
Velcro attachments are glued to the base. When dry honing, heat is generated. Heat can have a negative influence on the glue, softening it. Once soft, the adhesion properties are reduced and the tool separates making it useless.
The bond material is also critical. It must be strong enough to hold on to the diamonds but still wear away exposing fresh particles. Months of testing to figure out the tool’s durability must be run.
The diamond particle used is especially important when producing a polished surface. What is seen most often is having poor and uneven particle gradation. If the tool is a 70-grit, it must only have 70-grit diamonds. During production, if the quality control is not tight enough, larger particles will be mixed in. The issue is that deeper scratches will be put into the surface than intended. These scratches will not be removed with further steps and show once polishing begins. The only way to fix this issue is to drop down below the grit that produced the deep scratch and re-cut the floor.
The quality of the diamond particle can also have a broad range. Uniform gradation, hardness, and shape all affect your work. Any of these will negatively affect the floor’s final appearance.
Conclusion
Like they say, you get what you pay for. With diamond tooling, this holds true. There are many overseas suppliers that flood our market with nice-looking tools but as soon as you use them, they don’t perform as well as higher-cost alternatives. Ensuring your diamond tools come from a quality-minded company is the simplest way to go. DiamaPro Systems manufactures high-quality diamond tooling. Our tooling has all been extensively evaluated on multiple projects attached to various grinders. Some diamond tooling will work better on certain-sized grinders – if you are unsure which diamonds will best work for your application and grinder, reach out to us for help!
We also supply grinders and industrial dust collectors, which provides us with the knowledge and experience to better select the correct tooling for your project. Matching tooling to your grinder will increase production resulting in higher profits.