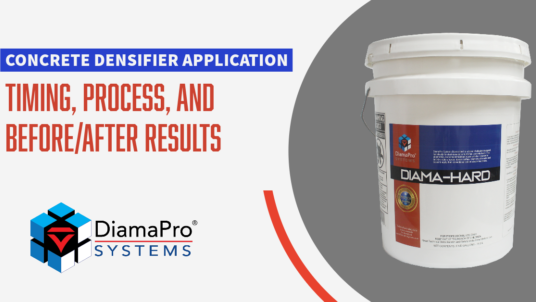
By applying a silicate to a marginal or moderately marginal concrete substrate, you will greatly increase the abrasion resistance of the surface. Concrete densifier application will also reduce the small void structure within the surface increasing its density.
On large concrete floors, there will be many truckloads of concrete used to produce the floor. Not every truckload of concrete will be the same. By utilizing a densifier after the concrete has hardened, you will be able to produce a more uniform floor when looking at abrasion resistance. This is very important when polishing the surface when selecting diamond tooling.
Understanding Concrete Densifiers:
Concrete is made up of water, cement, aggregate, and there can be admixtures. When water and cement are combined, the concrete hydration process starts. At that time, calcium silicate hydrate (C-S-H) develops. We can call it the glue that holds everything together and provides the performance characteristics of the hardened concrete itself. There is also a byproduct developed, calcium hydroxide, Ca (OH)2. This has no structural value to the hardened concrete.
Silicates take time to react. It’s a chemical reaction between two chemistries and this reaction does take time but some silicates will react faster than others. The most widely used silicates are Lithium, sodium, and potassium. There can also be a blend of two or three to obtain the benefits from each. Some are water-soluble. This means when they get saturated with water, they will become soft and might even liquefy.
The concrete densifer application reacts with calcium hydroxide producing calcium silicate hydrate, more glue. This is how you can increase the abrasion resistance of the surface and fill some of the micro pores within the surface. It will also aid in reducing “Dusting”. Dusting is when the weak surface is easily removed with minimal abrasion. You might have experienced this when walking across your basement floor and the bottom of your socks turn white.
Using a densifier on a troweled floor will extend the service life of the wear surface of a concrete floor. By increasing the abrasion resistance, the area that sees all the abuse is enhanced minimizing premature wear.
When placing an exterior concrete slab that will be broomed finished, a densifier will also strengthen the surface extending the life of the broom finish. Many acrylic sealers that are used to protect exterior concrete are compatible with the densifier.
When to Apply Concrete Densifier
If you are applying the densifier on a non-polished floor, it can be applied at any time after the concrete has reached its intended strength, typically after 28 days. The reason for this is to have enough calcium hydroxide developed in the concrete to react with the densifier.
When using a silicate within the polishing process, the time to apply depends on the substrate. There could be a time when the concrete strength is marginal. It is soft and the correct diamond tooling removes a lot of the surface. Saturating the surface with a densifier after the first grind might help harden the surface to enhance the grinding process. Many concrete floors also have different hardness across the floor. A silicate will help to create a more uniform hardness so the same diamond tooling can be used over the entire floor.
During the polishing process, there are contractors that densify after the 200 or even 400-grit resin bonded tool step. Some might even apply concrete densifier after both tool steps. Neither is right or wrong, it depends on the floor and the contractor’s preference. With some experience, you will know if an additional application will enhance your floor.
Concrete Densifier Application Process
Densifiers need to penetrate the surface of the substrate. To penetrate, the surface needs to be clean and free from any sealers, curing compounds, and other materials that could reduce the ability to penetrate.
Using an auto-scrubber on a troweled surface works well. If a curing compound was used to cure the slab, that needs to be removed. If it is a tilt-wall construction, a bond breaker might have been used, and that too needs to be removed. All dust and debris packed into the surface pores need to be cleaned out.
During the polishing process, the surface is ground with multiple diamond tools. No matter when you decide to apply concrete densifier, the honed area needs to be vacuumed well and auto-scrubbed clean before application. If not, the dust will be adhered to the floor once the densifier dries.
No matter if you have a troweled slab or polished surface, the application is the same. Using a low-pressure sprayer, apply enough material on the floor to completely saturate the surface. By keeping the floor wet for 20 minutes with the densifier and not allowing it to dry, you should reach full saturation.
Some densifiers contain a surfactant which is a wetting agent. Surfactants make water wetter to enhance the penetration of the liquid. These materials require no agitation to reach full penetration. Others, usually the lower-cost densifiers, do not contain a surfactant. These materials need to be worked into the surface with a broom or mop to break the surface tension allowing penetration.
The average concrete slab will reach full penetration at an application rate of 400-600 sq.ft./gallon. Be cautious to not allow the densifier to puddle and dry. If allowed to dry in a puddle, a white crystal of film will develop that must be mechanically removed.
Maintenance and Long-Term Benefits
A densified troweled floor is easily maintained. Using a pH-neutral cleaner in an auto-scrubber fitted with a diamond-impregnated pad works well. This type of cleaning can be performed on a regular basis keeping dirt and abrasives from damaging the floor.
With a polished floor, the same pH-neutral cleaner in an auto-scrubber fitted with a diamond-impregnated pad also works well. If a film-forming or penetrating protective guard has been used, contact the manufacturer of the guard for maintenance instructions.
Typically, reapplication will not be needed. Densifiers are permanent. They will not peel or scratch off the surface. The only way to remove them is to remove the concrete they have reacted to. If another application is on a troweled concrete surface, clean the floor extremely well and reapply in the same manner as initially applied.
Densifiers can be used on a troweled, broomed, or polished concrete substrate to enhance the abrasion resistance which increases the service life of the slab. They are a low-cost solution if you are interested in increasing the durability of the concrete surface. They can be used on interior and exterior projects.
Before application just clean the concrete slab from any material that would impede penetration. Using a low-pressure pump sprayer to apply is a low-cost, effective method.
When polishing concrete, a densifier will enhance your process and help you obtain a higher DOI (distinction of image) and gloss. A harder surface is just easier to polish.
Diama-Hard and Diama-Hard Plus with Microban Product Protection from DiamaPro Systems are available in 1 and 5-gallon options. Check out the features below:
- New construction, existing concrete slabs
- Hy-bred polished floors where only transitional and resin tooling or diamond-impregnated pads are used
- Dye-enhancing properties to brighten colors
- Stabilizers to minimize the effect of ultraviolet light on dye
- Enhanced concrete surface dust reduction
- VOC Compliant, reduced odor and non-flammable
- Aids in the reduction of ASR and efflorescence
- Non-dilutable with water