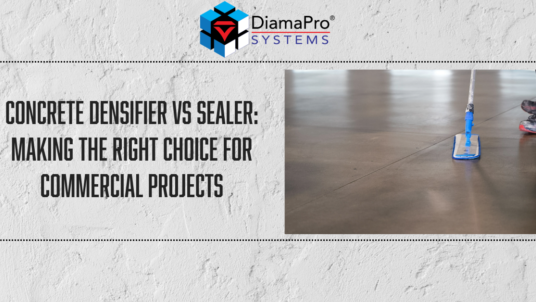
Protecting the floor while increasing its service life should be a high priority. There are multiple ways to approach the floor but first, the type of potential damage needs to be determined. If harmful chemicals are involved, a protective film-forming coating is recommended. If abrasion from traffic is a concern, applying a liquid hardener and polishing the floor might be an option.
What are Concrete Densifiers?
Concrete densifiers or liquid hardeners are used often to increase the abrasion resistance of a concrete floor. These materials are applied to a properly prepared, cured concrete floor.
During the concrete curing process, a chemical reaction takes place. When combining water and cement, the hydration process starts. When concrete hydrates, there are several chemicals produced. The most important one is Calcium Silicate Hydrate, the glue that, when the concrete has cured, holds the aggregate and sand together. The more Calcium Silicate Hydrate that is produced, the higher the concrete strength and abrasion resistance becomes.
During the hydration process a by-product, Calcium Hydroxide, is also produced. Calcium Hydroxide has no structural value on its own in the hardened concrete. When a silicate (densifier, liquid hardener) is applied to the surface of cured concrete it reacts with Calcium Hydroxide. This reaction produces more Calcium Silicate Hydrate. As mentioned before, the more Calcium Silicate Hydrate there is, the more durable the concrete will.
Since the liquid silicate densifier is only applied to the surface, it can only enhance the concrete’s strength as deep into the slab as the material will penetrate. This will not increase the strength deep, within the concrete, it only strengthens at the surface. That is exactly where you need it when addressing abrasion resistance.
What are Concrete Sealers?
Concrete densifiers offer minimal protection from chemical attack. By selecting the appropriate concrete sealer, you can protect the concrete substrate from almost any chemical. There are thousands of options when it comes to concrete sealers. You can select urethane, acrylic, polyaspartic, epoxy, and the list goes on. Many factors will influence your selection.
Concrete sealers are topically applied over a properly prepared concrete surface. Once cured they develop a protective film on the surface. The level of protection the sealer offers will depend on the chemical makeup of the sealer, the chemical itself, how long the chemical will be in contact with the floor, and the temperature of the chemical and environment, along with several other factors. The best way to determine which sealer is the best for your project is to have a mock-up installed and evaluate the chemical resistance using the exact chemicals in your facility. Not only assess the individual chemical but if more than one could mix with another when contacting the floor, include that combination also.
Making the Right Choice for Your Commercial Project
The right choice for you might be different than the choice someone else might make. The system selected should be based on what the intent of the system will be.
If increasing abrasion resistance is the result you are interested in, a densifier or liquid hardener is the way to go. It is easy to apply, will enhance the abrasion resistance of cement-based substrates, and is low cost. It will also fill some of the micro pores at the surface increasing the water repellency. It is not to be confused with a true water repellant but will reduce solid water (not water vapor) from penetration.
When protecting the concrete substrate from chemical attack, a film-forming coating or sealer should be selected. Once cured, it develops a surface film blocking a chemical from contacting the concrete substrate. Not all sealers or coatings will withstand every chemical. This needs to be determined with an in-place mock-up in your facility. Many sealer and coating manufacturers will publish chemical-resistant charts on their technical data sheets, and this is an excellent place to start the search. Remember, these tests are all performed in a lab under lab conditions. That means the ambient temperature and humidity are held at a constant value. The temperature and humidity might not be the same in your facility. These two important values will have an impact on the protection system you select.
The working environment the sealer or coating will be in also impacts the selection. Forklifts, foot traffic, or any high abrasion situation. This could wear away a substantial level of initial protection, reducing the service life of the system.
What to do Next
Reach out to DiamaPro Systems to provide additional guidance while selecting the best system for your situation. Although not every manufacturer will have the ability to provide a solution for every scenario, DiamaPro Systems has the knowledge to point you in the right direction.