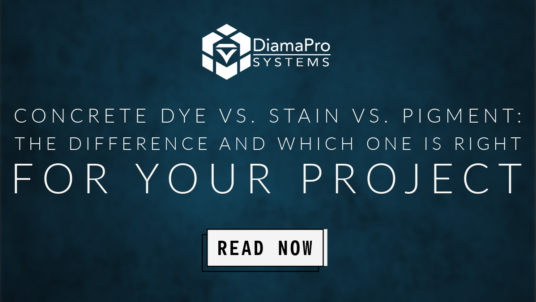
Geographically, terminology plays a big part in describing available coloring methods. In the west, dyes might be called stains. In the east, dyes might be used to color fresh concrete. Is there one term right and the other wrong, no. It’s better to describe what is required and not use a single descriptive word.
The primary coloring methods used include dye, stain, and pigment. Each one has its own architectural flair. Dyes will have a translucent appearance. They will show the natural characteristics of the concrete slab but colored. Stain can also be somewhat translucent, but it will appear almost opaque if multiple coats are applied. Pigments, also called integral colors, are induced into the concrete prior to placement. It colors the cement paste, producing a solid color without appearing “painted.”
What is Concrete Dye?
DiamaPro® Systems produces concrete dye, DiamaPro® Diama-Color, a translucent coloring method typically used in the polishing process or when dying a sealing is called for. Dyes consist of a dye particle and a carrier. The particle can be produced in a multitude of colors. The carrier is the liquid that allows the dye to penetrate the concrete substrate. The appearance will look modeled and non-uniform.
Carriers are solvents. They are not all equal in performance characteristics, but each is especially useful. Water, in chemical terms, is a solvent. Compared to the other solvents that can be used, it evaporates much slower and has a higher surface tension. The slower evaporation allows the installer time to spread the liquid dye, producing a more even, colored appearance. The higher surface tension reduces the level of penetration compared to the other solvents that are typically used. This is not an issue if the installer understands it. When polishing and using water as the carrier, a small amount of the surface will be removed after the dye has been applied. This will reduce the colorants’ intensity but not completely remove it.
Acetone is a V.O.C.-exempt solvent. This means the EPA (Environmental Protection Agency) does not recognize acetone as harmful to the atmosphere once it evaporates from the surface. Acetone flashes (evaporates) very quickly. Using acetone as the carrier will allow the installer to move quickly through the project without waiting for the dye to dry. Acetone has an extremely low surface tension. This allows for easy and deep penetration.
Once the dye particle is mixed with a carrier, it starts to break down. Eventually, it completely dissolves and becomes a solution. This solution absorbs into the surface. As the carrier evaporates, it leaves the dye particle behind coloring the surface. There will be no noticeable film to scratch or peel. The concrete surface will not change physically, only in color.
Dyes colors will not be vibrant. One thing to remember, they are translucent, and the color of the concrete substrate will impact the final color and show-through. The lighter the color of the substrate, the more vibrant the dye color will be. If using white cement in the concrete or overlay mix design, the color will have more of a color pop. If a true representation of the final color is needed, the only choice is to install a mockup using the same process as the project. The mockup location needs to be on a slab next to the work area but not on the area that will be stained.
Dyes are not UV stable. Under intense sunlight exposure they will eventually fade. When installing a dyed system on an interior floor project, there might be windows that allow sunlight into the area. Windows have glass. Newer glass panes have UV-reducing properties. This will minimize issues when using dye.
What is Concrete Stain?
Stains are another method to color concrete. Again, the term stain can encompass a large group of material types. Stains will hold pigment. Pigment is a large, non-soluble particle that comes in a multitude of colors. Pigment is usually UV stable and that means it can be used on exterior projects.
Stains have a binder that will bond the particle to the substrate. This bond can be mechanical or chemical. Mechanical binders such as acrylic, urethane, or epoxy are film-forming colorants. A chemical bond, such as DiamaPro® Diama-TLC, chemically reacts with concrete creating a strong bond.
Stains can be opaque in appearance. This might take multiple coats to cover the substrate. Stains can provide a modeled appearance, but they will not do this on their own. Think of it as painting a wall with conventional wall paint.
What is Concrete Pigment?
Straight pigments can be used when coloring concrete. A pigment, or integral concrete color, is induced when the concrete is being produced. It can also be considered a concrete admixture. Integral color colors the cement paste. It uses the gray color tone of the cement to produce a wide color range from lights to darks.
Concrete Dye vs. Stain vs. Pigment: Key Differences
When selecting a coloring method the client’s expectations must be found. The final appearance, substrate condition, environment, and color choice will affect the decision.
If the client is looking for a natural, colored polished appearance for their existing floor, using dye will most likely be the selected coloring method. Dyes will not look painted and are designed to be applied during the polishing process. The final color will be soft and translucent. DiamaPro® Diama-Color is produced in a wide range of colors. When polished, the showing aggregate will remain its natural color, only the cement paste will accept the dye. Dyes are not UV stable and should not be used in exterior applications.
If starting off with a new concrete slab and the concrete has yet to be placed, an integral colorant can be used. This method is the most durable of all choices. Using an iron oxide pigment the final color will be color fast and show minimal fading over time. Conventional gray concrete will show the color of the cement that is used. There is no color standard a cement manufacturer needs to follow. Whatever the color of the cement is, the floor will be similar. Integral color will narrow the final color range, producing a much more uniform overall appearance. You would think since the color of cement is gray, the final color will be gray. It might be, but there are a substantial number of shades of gray. One area might be light gray, another medium gray, and another dark gray. To close the color gap throughout the job or to be able to specify a specific color, an integral gray colorant should be used.
When working on an old, existing concrete floor, there could be a need for repairs. Repairs can be tricky to conduct if they need to go unnoticed. Using an opaque stain will hide the color difference of the repair. The repair can be completely camouflaged if the texture is the same as the surrounding area. Stains will not fill in defects, only add color.
All these methods produce color. Dyes absorb into the surface leaving no film so they can be polished. Integral color pigment is also polishable. It is induced as an admixture into concrete as it is produced. Once the concrete has been cured, the color is permanent. Pigmented stain cures more on the surface. These are surface colorants and that is the reason they produce a uniform color appearance even though there might be repairs.
The chosen color might lead you to a specific coloring method. If bright, vibrant colors are in the design, a pigmented stain will be an excellent choice. Using a pigment to color a stain offers almost unlimited color options. It has similar characteristics to typical wall paint. They both use pigment to provide color, a binder to hold the pigment, and offer the ability to bond to a substrate.
If a subtle color is needed, dye and polished or sealed system should be considered. Dyes blend with the cement color without hiding or covering the natural beauty of the substrate. Multiple colors can be used at one time and the amount of color can be adjusted to fit within the design.
Integral color was initially used on exterior projects. Streetscapes, hardscapes, medians, and sidewalks were the first project types. It can add color to any concrete mix design. Whether concrete is being used in an eight-inch-thick slab for a highly traveled street or at a four-inch-thick in a street median that experiences no regular traffic, the UV stable color will be the same. The range of color is wide but will be affected by the color of the cement. When formulating integral color, the cement color is always taken into consideration. When using gray cement, a gray hue will be shown in the final color. Bright reds, greens, and yellows will never pop like they do when using a pigmented stain. Medium to dark color is less affected by the color of the cement. If a brighter color is desired, white cement can be used. White cement is not regularly available at a batch plant. It is a special cement blend that will need to be shipped in just for the project. This will dramatically increase the cost of each treated yard of concrete by as much as three times. On large pours, this can drive the cost of the treated concrete out of budget.
There have been interior projects that have chosen to use integral colored concrete. Of course, these are projects that are placing a new slab or using a cement-based overlay system that will accept integral color. Grocery stores, entertainment venues, office buildings, and residential homes all have used colored concrete in their projects. The color will be the same throughout the floor. The only color difference met will be caused by the finishing process. The concrete needs to be designed, placed, finished, and cured in the same manner throughout the project. If that’s done, the color will be uniform. Once cured, these projects can be polished or sealed with a protective sealer.
Choosing the Right Solution for Your Project
Selecting a coloring method will be based on a few factors. The age and condition of the concrete substrate, color choice and intensity, color opacity, and environment will all affect your selection.
When approaching the project, the condition of the slab must be evaluated. If it’s a new pour, all methods can be used. If not, integral pigment cannot be used. What color are you looking for? If it is a bright, vibrant color, a pigmented stain will get you there. With natural, softer colors, all methods will work.
The environment will always play a part. Is this an interior or exterior project? Will there be any harmful chemicals that will be in contact with the finish floor or constant, heavy, and abrasive traffic? Dyed and polished concrete is suited for abrasion but not chemical attack. Stained and sealed will hold up well in a chemical environment with the proper sealer. Integral colored concrete can be polished or sealed so this would be a good fit under both scenarios.
There are projects where design will be the driving factor. Unfortunately, it shouldn’t be, but it is. Just because the designer calls for a translucent colorant, doesn’t mean it will perform well. If the floor has been patched or there are splotches of coarse aggregate showing throughout the floor, these will affect the final appearance. The coloring method needs to match up with what there is to work with. If it doesn’t, the success rate will be minimal.
Conclusion
Dye is a penetrating, translucent material well suited to be used in the polishing process. If desired, dyes can also be sealed with an array of protective coatings to resist all forms of chemical attack.
A pigmented stain offers a large color palette. White, black, bright, and soft colors can be obtained. It will look “painted.” The film-forming material will hide the color of the substrate. But if the designer is calling for a monochromatic appearance, it is an excellent choice. When working with pigmented stains, they all need to be sealed.
Integral color will take multiple tradesmen to install. During placement, a concrete finisher will be needed. They will place the colored concrete and finish it to the desired finish. If it’s going to be polished, a polishing contractor will need to come back in 28+ days to complete the work. If sealed, the concrete still needs to be cured sufficiently to meet the sealers’ requirements. This too will need an added contractor.
DiamaPro® Systems produces dyes and pigmented stains. If integral color is the direction taken, Niagara Machine, the DiamaPro® Master Distributor, can be of help.