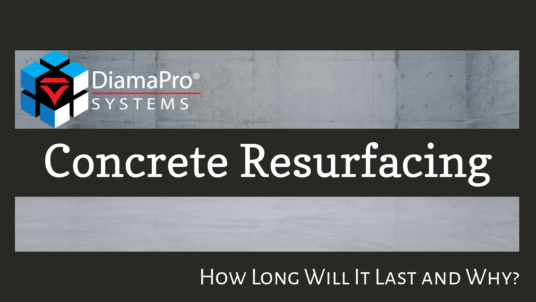
There are a vast number of resurfacing systems available. The final expectations will dictate which one to select. When evaluating a resurfacing system, the number one concern is longevity, or how long it will last. Factors that will impact the service life of a system include the environment the system will be in, the quality of the existing substrate, and maintenance. The selected system is based on these factors.
What is Concrete Resurfacing?
First, evaluate the substrate for suitability. Is it in good enough condition to support a resurfacing system? An owner could feel that retaining the original substrate will save money. There will be scenarios where a jackhammer might be the best option. The subgrade needs to support the intended loads. Complete removal might be less expensive overall if there are structural cracks throughout the slab.
Preparing the surface to accept the system is of the utmost importance. The systems’ manufacturer should have a written recommendation. They provide instructions on what they need to obtain the highest level of performance. As an owner, I would always request the Technical Data Bulletin for the system from the installer and read it thoroughly. This knowledge might help justify the installer’s process and reduce your stress level.
Most resurfacing materials come in two-component units. The material might be pre-colored or come with a color pack. The installer will combine an A and B component in a mixing vessel and then, if needed, add the color per the manufacturer’s instructions. With the correct mixing paddle, blend all components. The amount of material mixed will depend on the system selected, ambient temperature, square feet resurfaced, and number of workers placing the system.
Once placed, apply the final texture. Broom-finished, imprinted with a stone texture, and smooth-troweled, are a select few. The owner will determine this.
Once the system has cured, a topical sealer that the material manufacturer recommends will provide additional stain protection and color enhancement. These sealers not only offer additional protection but also provide an easier-to-clean surface. No matter which sealer, they are a maintenance item that must be reapplied every 2-5 years to retain their performance properties.
Factors Affecting the Longevity of Concrete Resurfacing
The possible issues with a resurfacing system can be delamination, cracking, abrasion, color fade, and staining. Each of these can point to the source that produced the issue.
Delamination is when the material releases from the substrate. Surface preparation can be the culprit when investigating the possible cause. Surface preparation entails not only roughening the surface but also the removal of all bond-inhibiting materials. Oil and grease can lead to a bond failure. Cracks can also allow water to penetrate the resurfacer and accumulate at the bond line. During freezing temperatures, water turns to ice and expands. This expansion can apply enough force to cause a delamination.
There are two types of cracks, moving (dynamic) and non-moving (static). Fill static cracks with repair material before applying the resurfacer. If the cracks are moving, reflect them through the resurfacer allowing for continuous movement. If filled with repair material and coated over, a crack could develop later in the resurfacer right over the dynamic crack once it moves again.
There are resurfacing systems designed to enhance the abrasion resistance of the substrate to withstand vehicle and continuous foot traffic. If installed in the incorrect environment, surface wearing will show loss of color or fine aggregate exposure.
There are methods to add color to a resurfacer. Ones recommended by the system manufacturer will be color-fast. Ultraviolet light or water washing over the cured system should not affect the color. If color degradation appears, make sure the installer used an approved coloring method.
Protecting the installed system is imperative to enhance stain resistance. Sealers will block the most common staining materials. The key is to block stain-causing liquids from reaching the resurfacer. Always use what the manufacturer recommends for your project. Having a good cleaning process will also help. Once the liquid has spilled on the surface, remove it as soon as possible to minimize any issues.
Typical Lifespan of Resurfaced Concrete
A typical resurfacing material should last 10-15 years. This is quite common. If it is in an environment suitable for the system, issues will only rear their head when one or more factors listed above happen. Cracks and delaminations are the most prevalent. Both have little to do with the actual product, they are due to the installation practices the installer follows. Installers are all human; they can make mistakes. Unfortunately, the homeowner owns these mistakes once the installer is offsite. Selecting an experienced installer with a list of high-end references is a suitable place to start. Call all the references provided and consult with the Better Business Bureau. Contacting the Distributor where the installer buys their material might also reinforce your installer selection. They could provide valuable information.
A well-designed, installed, and maintained conventional concrete slab will last years. High cement content, low water-to-cement ratio, properly cured and finished will provide a long service life. A quality resurfacer applied to a quality substrate should be no different. But if the substrate is not of high quality, the resurfacer’s life span will be short.
Tips to Extend the Life of Resurfaced Concrete
The number one way to extend the life of a resurfacer is to secure the services of a quality installer. The methods they use to install the system will have a direct impact on the service life of the system. You can select the best available material and still have a failure if not installed correctly.
There is no such thing as a maintenance-free system. Maintaining a resurfacer might only be providing a good cleaning twice a year. Sealers do not last forever. They need to be reapplied when showing wear or loss of color. If this is beyond your capabilities, ask the installer if they offer a resealing program. No matter how or who does it, it is a way to extend your service life. If the sealer wears to the point where the resurfacer starts to wear, the repair will be more costly and extensive and will never exactly match the surrounding area.
Conclusion
Resurfacing a concrete slab can add value to your property. It can add an attractive surface emulating large sheets of stone or a uniform-colored wear surface. If conventional gray concrete is not what you want, multiple resurface systems are available. These systems are not only beautiful but can also provide an increase in durability.
The long-term usefulness of a resurfacer hinges on the installation of the system. Selecting an installer with experience is critical. They will have a good understanding of which system is right for your application. What works in Florida might not work in Montana. If you are having problems locating a quality installer, DiamaPro® Systems works with installers in your area. We have experienced field representatives spread throughout the country. Each one has a vast level of knowledge that will aid in selecting resurfacing systems.
DiamaPro® supplies installers with surface preparation equipment, crack repair materials, and resurfacing systems. We can help by recommending a top-notch installer for your project.