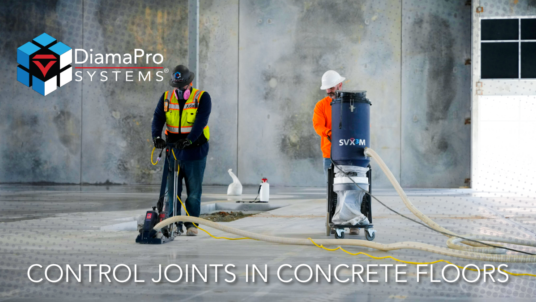
Concrete is a rigid material. When flexed or stretched, it will break. To increase flexural and tensile strength, reinforcing steel is placed in the slab. Concrete has great compressive strength and manages heavy loads. When under a compressive load, you will not see it crush in a normal working scenario. Its hardness and high compressive strength are why it is used in every construction project.
Unfortunately, all concrete floors move. During the hydration process (curing), it shrinks. A normal concrete mix design has twice the water needed to develop into a hard mass. The added water allows it to flow during placement. As the water evaporates, the concrete loses volume. The reduction in size places stress on the slab and cracks develop due to this internal stress.
Control joints are not designed to move but have the ability to move if necessary. They are weakened planes cut into the slab, providing a predetermined location for the shrinkage to take place, reducing random, unwanted cracks. Concrete will crack at the point of least resistance in the slab. Cutting control joints into the slab creates a weak area which directs or funnels cracking due to shrinkage. Control joints are placed in a grid pattern at a calculated depth. According to the American Concrete Institute (ACI), the spacing is 2.5 times the thickness of the slab in feet. Example: 6” slab times 2.5 equals 15. The spacing will be every 15’. The depth of the cut needs to be deep enough to create a weak plane. ACI recommends the depth to be 25% of the slab thickness. With a 6” slab that will be 1.5”.
Control Joint Filler
Control joint resins have specific performance properties that lend themselves well when used to fill control joints. The mixed material must flow to the joint's bottom without any external force. The material should come pigmented or be able to be tinted on the job site. Having a complimentary joint color can add to the aesthetic appeal of the interior design.
Control joints are placed or cut into the slab every 10’-15’. This means there will be open voids that will collect dirt and harbor harmful microbes. Forklift traffic also impacts the service life of the floor while driving over open control joints. When a forklift rolls over a joint, the wheel affects the joint shoulder. The impact can be so violent that concrete breaks away. The damage caused by wheel traffic can cost thousands of dollars to repair and damage forklift wheel bearings taking them out of commission. The cured material is hard with a Shore A hardness of 80+, with the flexibility to perform properly in this environment.
Control joints are considered stable, but they will eventually show some movement. Filling them with a 100% ridged material will only lead to joint failure or slab cracking next to the joint. A semi-ridged polyurea joint filler such as DiamaPro® Diama-Joint 2.0 will keep the joint clean and allow forklifts to roll over them without depressing into the joint, reducing joint shoulder deterioration. It creates a bridge from one shoulder side to another. Control joint filler is hard but with marginal flexibility. The joint is filled full depth to the bottom, providing support to the filler. When the filler is shaved level with the concrete surface, forklifts can roll across the joint without affecting the joint shoulders.
The strength of the bond of the joint filler is also critical. Concrete has a tensile strength of approximately 10% of its compressive strength. A 4,000-psi slab will have a tensile strength of 400 psi. Having a joint filler with a lower bond strength than the concrete’s tensile strength will save the joint shoulders from deterioration during movement. If the filler has a higher bond than the tensile strength, the filler will not release, and concrete cracking will occur along the joint.
Surface Preparation
The preparation or cleaning of the surface when bonding two materials together is critical. Bond-inhibiting materials only cause problems. With control joint fillers, it is exceptionally important. The bond strength of a control joint resin is low to begin with. The reason for this is when the joint moves and opens, you want the bond between the joint filler and joint shoulder to be the weakest link and separate. Separating relieves the stress on the concrete and reduces concrete damage. If a high-bond strength material is used, the concrete will crack along the joint leading to expensive, concrete repair.
The surface preparation method is mechanical. A chemical prep method should never be considered. Two mechanical processes have been used successfully to clean joints. Running a sandblaster down the joint will clean, abrade, and blow out any foreign materials from within the joint. This method is what is used on large exterior paving projects where appearance is not as critical as performance. The blast area will extend beyond the joint sides and appear different.
For interior control joints, appearance and performance are important. Care must be taken not to disfigure the concrete surface on each side of the joint. A concrete joint saw fitted with a diamond joint blade will perform this work. Once inserted into the joint, this blade abrades both sides of the joint. It not only removes all bond-inhibiting materials, but it also shapes the joint into the ideal shape for best performance. After running the blade down the joint, vacuum well to ensure a clean surface.
Conclusion
There is more than one type of concrete joint. They all have their use and must be filled with the proper joint filler. A control joint reduces slab cracking, allows slab movement, and directs shrinkage to a predetermined location.
There will be more control joints in a slab than any other type. They are not designed to move, but some movement is expected. Control joints run across aisleways where forklifts move back and forth. If these joints are left unfilled, they will show some joint shoulder deterioration once put into service. A control filler will dramatically reduce this.
DiamaPro Systems manufactures surface prep equipment, chemicals, and tooling for polished concrete and resinous coatings. We have the experience and knowledge to guide you through the joint-filling process. Control joint resins, dual component joint fill pumps, and joint saws and blades, we have it all. Give us a call to request a demonstration. You will be pleasantly surprised by how easy the system is to use and how it can help you enhance the performance of your clients’ floors.