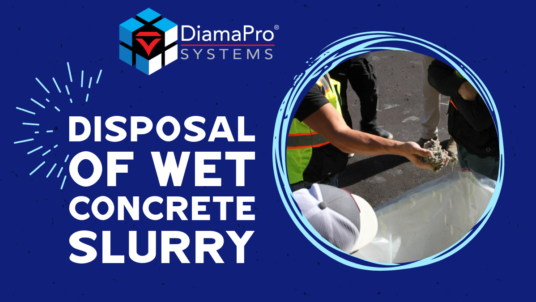
Concrete Slurry Concerns
There are concerns when disposing of wet concrete slurry. The first is from the concrete particles that are suspended in the water. They can hold contamination that must be kept and not allowed to seep from the slurry once disposed of. The contamination could consist of metals, semi-volatiles, or volatiles.
Concrete has a naturally high pH value. The value begins around 13 when the concrete is freshly placed. Under normal conditions, it will gradually drop down to 10.0-11.5. Carbonation and chemicals will lower the pH level. This drop in value happens in years and not days. When the slurry water mixes with the ground concrete particles, the pH of the water will increase to a value equal to that of the concrete. If this high pH value water seeps into the groundwater, it has the potential to contaminate streams, rivers, and the underground aquifer.
Equipment Needed
Slurry Extraction System
- Once the concrete slurry has been generated, it needs to be extracted from the floor. Whether it be to pick up slurry from around a freshly bored hole or a 10,000-square-foot floor, there needs to be a method of removal.
- Caution: never allow the concrete slurry to dry during the removal process. It will be more difficult to remove.
- Wet-Dry Vacuum
- A small, portable wet-dry vac fitted with a squeegee wand will work well for small areas.
- Slurry Vacuum
- A slurry vac is a 110v powered wet vac fitted with a front-mounted squeegee. While running, it is manually pushed across the slurry-covered floor pumping the wet slurry into a recovery tank.
- DiamaPro® WVX vac
- Lightweight – 70 Lbs.
- 20-gallon recovery tank
- 32” U-shaped squeegee
- Collect water and slurry over the entire squeegee.
- Comes with a squeegee with a wand and hose for hard-to-reach areas.
- Auto-Scrubber
- Auto-scrubbers come in varied sizes, but they all do the same thing.
- Large ride-on scrubbers for large projects
- Small push models that fit better on small projects.
- They have a brush system to scrub the floor, a freshwater tank applying water to enhance the pickup, and a recovery tank to capture the debris.
- While moving, the brush system with clean water agitates the slurry.
- Immediately in the back of the machine, the squeegee extracts the debris from the surface pumping it into the recovery tank.
- DiamaPro® Scrub 20 auto-scrubber
- Manual walk-behind
- Battery powered.
- 230 Lbs.
- Brush width – 20”
- Squeegee width – 30”.
- 13-gallon freshwater tank
- 15-gallon recovery tank
Slurry Transfer Pump
- Once the recovery tank is full, the slurry needs to be pumped out.
- The pump needs to manage not only water but also thick, abrasive concrete slurry.
- DiamaPro® Slurry-Spout
- A venturi-type pump connected to a pressure washer. This is a nonmechanical pump system that can transfer large particles with ease. There are no mechanical parts to break or wear out.
- The DiamaPro® Slurry-Spout connects to the wand of a pressure washer without changing the fittings on the pressure washer.
- A pressure washer that produces a minimum of 3 gallons of water flow is required.
- It increases the water flow of the pressure washer by tenfold.
- With a pressure washer that produces 4 gallons per minute, the Slurry-Spout will transfer concrete slurry at 40 gallons per minute.
Filter Bag
- The concrete slurry at this point is mostly water.
- Filter bags come in assorted sizes to accommodate the amount of slurry being generated.
- As the treated concrete slurry is transferred into the filter bag, the water and concrete particles will separate. The water will penetrate through the filter bag while keeping the slurry cake.
- DiamaPro Slurry-Sifter
- Slurry-Sifter is a durable felt-lined bag that allows water to penetrate while keeping the solids held within.
- It has heavy-duty forklift lifting stirrups that wrap completely under the bag to make for easy and safe removal.
- Fill the Slurry-Sifter no more than ¾ full to allow maximum water filtering.
Storage Vessel
- The filter bag cannot stand on its own. It needs to be held up for ease of use.
- The ridged storage vessel is designed to support the filter bag allowing for proper drainage.
- The vessel has connections at each corner to attach the filter bag.
- DiamaPro Slurry-Vault
- The Slurry-Vault is the support system for the Slurry-Sifter
- The Slurry-Vault is constructed out of durable polyethylene.
- Forklift slots are inserted at the bottom of the Slurry-Vault for ease of transportation.
- It will safely hold a tremendous amount of concrete slurry that needs dewatering.
Accessories
- 4 oz measuring cup
- Measure Slurry-Splitter
- Pressure Washer (3+ gal/minute output)
- Connect to Slurry-Spout
- 1-gallon bucket
- To hydrate Slurry-Splitter
- ½” drill with paddle
- Mix in Slurry-Sponge
Chemicals Needed
- Flocculent
- The water in the slurry will not filter efficiently through a filter bag without help.
- A flocculent aids in the separation of water from the solids in slurry.
- DiamaPro® Slurry-Splitter
- Slurry-Splitter is a flocculent material.
- Reduces the pH level of the slurry.
- Concrete particles are negatively charged, and the Slurry-Splitter is positively charged.
- Like a magnet, positive and negative charges attract.
- The Slurry-Splitter grabs ahold of the concrete particles, separating them from the water.
- The water then filters through the Slurry-Sifter bag.
- Solidifier
- Paint Filter Test
- Finds if all the water in the slurry cake has been captured.
- Once the solidifier has been induced, put some of the cake into the paint filter.
- At that point, there should be no water exiting through the filter.
- A solidifier is a superabsorbent material that can encapsulate many times its own weight in water.
- After the slurry has been separated from the water, some residual water will remain.
- Sprinkle the solidifier on the residual water and mix.
- The remaining captured water will absorb and mix into the slurry cake.
- DiamaPro® Slurry-Sponge
- A solidification agent
- Encapsulates free water.
- Used to absorb the remaining water producing a very dry cake that will reduce leaching in the ground.
- Sprinkle Slurry-Sponge on top of the cake contained in the Slurry-Vault.
- With a 1/2” drill and paddle, mix into the cake. Immediately the cake will become dry.
- At this point, the cake is ready for disposal.
- Paint Filter Test
- Equipment Cleaner
- When wet grinding, cutting, or drilling, the equipment will become coated in concrete slurry.
- Even if the equipment is rinsed down, concrete film will remain.
- DiamaPro® Slurry-Scrub
- Applied with a foam gun attached to a pressure washer.
- Once applied, it breaks down concrete film.
- Will not harm metal or plastic components.
Slurry Containment Process
Step 1
- Locate a dump site that will accept the final slurry cake.
- There might be regulations they follow and should be able to supply them to you.
- What tests, if any, will they need to be performed on the dry slurry cake.
- Some facilities need no testing at all.
Step 2
- Insert the filter bag (DiamaPro® Slurry-Sifter) into the vault.
- Attach the bag to all four corners of the container (DiamaPro® Slurry-Vault).
Step 3
- Decide the size of the auto-scrubber recovery tank.
- Add 4 oz. of DiamaPro® Slurry-Splitter into a gallon of potable water to treat every 20 gallons of concrete slurry recovery from the recovery tank.
- If the recovery tank is 40 gallons, hydrate 8 oz. of Slurry-Splitter.
- Allow it to set for a minimum of 15 minutes in a bucket with water.
- Pour the hydrated Slurry-Splitter solution into the recovery tank of the auto-scrubber and begin extracting the slurry from the floor until full.
Step 4
- Connect the Slurry-Spout to a pressure washer.
- Insert the Slurry-Spout into the recovery tank.
- Activate the pressure washer and pump the slurry into the Slurry-Vault lined with the Slurry-Sifter.
Step 5
- The amount of water in the slurry will depend on how fast the dewatering will take.
- If a large amount of slurry is being generated, potentially a second or even third container system might be needed.
- As the water filters through the filter bag, pump out the filtered water.
- The filtered water can be reused in the auto-scrubber or disposed of.
Step 6
- There will be residual water on the surface of the slurry cake after the dewatering has taken place.
- Sprinkle the solidifier (DiamaPro® Slurry-Sponge) on the cake.
- With a ½” drill and paddle, mix the solidifier into the damp cake.
- Repeat if not all water has been absorbed.
Conclusion
Cement slurry management when wet grinding, drilling, or cutting concrete is the responsibility of the contractor generating the slurry or, if outlined in the contract, the General Contractor. Having the correct tools and chemicals allows for easy management. DiamaPro® Systems has developed this system to aid in safe slurry disposal.