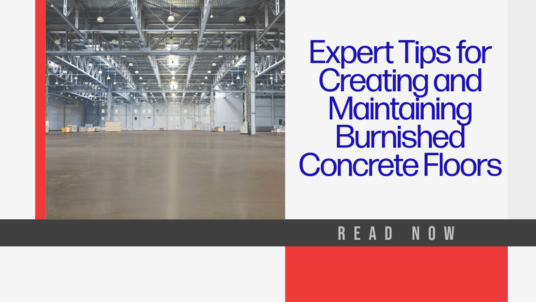
A floor’s final surface finish dictates its suitability for its intended use. The surface needs to withstand abrasion from foot and wheel traffic. Whether the slab is 8” thick or 4” thick, the wear surface has the same abrasion resistance so long it is finished in the same manner.
There are burnished concrete finishing techniques that will increase the abrasion resistance of the concrete surface when compared to a finishing process normally performed when the slab is placed. Once the concrete has been cured, other mechanical processes can also be done to increase the abrasion resistance.
When increased abrasion resistance is the goal, the appearance will also be enhanced, and the ability to clean the surface will be elevated. That is why a “burnished” floor has been the top choice for industrial and commercial facilities worldwide.
What is Burnished Concrete?
Providing an extremely smooth surface is of the utmost importance when the goal is to increase surface abrasion. A smooth surface will show little to no abrasion from foot or wheel traffic.
During concrete placement, a power trowel is used in the final finishing stages. This tightly compacts the cement and fine aggregate producing a hard, dense wear surface. If the final finish is properly performed, the power trowel can also produce an exceptionally smooth, abrasion-resistant surface.
During or after the concrete finishing process, a chemical hardener, such as DiamaPro® Diama-Hard, can also be applied to increase the hardness of the surface. DiamaPro® Diama-Hard reacts with the calcium hydroxide within the concrete producing more calcium silicate hydrate. This is the glue that holds the concrete together giving it its strength.
Once the surface has been finished, leaving it extremely smooth, a diamond-impregnated burnishing pad, like the DiamaPro® Sparkle Pad, can also be used to enhance the abrasion resistance when used with DiamaPro® Diama-Hard. Sparkle Pads are produced with different diamond grits. The first steps are performed with a coarse grit pad, producing an even smoother surface. As you move through the grits and finish with an ultra-fine grit, the surface will become ultra-smooth. These pads can be used dry on a high-speed burnisher or wet on an auto-scrubber. This system can also be used to maintain a burnished surface.
Using diamond abrasives to polish the surface is the ultimate procedure to produce a burnished, abrasion-resistant floor. No matter how the concrete was initially finished, the surface will become exceptionally smooth. Polished concrete is produced using diamond abrasive tooling. It starts with a coarse tool to remove all large to medium-sized hills. Once those are flattened, the next diamond tool will flatten the floor even more. This process continues for a few more tooling steps until the surface has developed a high gloss. The gloss level will correlate to the smoothness of the surface. The smoother the surface, the more abrasion-resistant it will be. During the polishing process, DiamaPro® Diama-Hard is also used. This will increase the surface hardness to not only increase the abrasion resistance but also enhance the polishing process.
Benefits of Burnished Concrete Floors
No matter which burnished concrete floor method is selected, they will all increase the abrasion resistance of the concrete surface. Some of the main factors that could influence your decision are durability, aesthetic appeal, maintenance level, and cost-effectiveness.
Burnishing with a power trowel during the concrete placement needs to be done upfront before the concrete is cured. This is the least expensive method because it’s performed by the concrete placing crew. There will be no added mobilizations from an outside contractor and the equipment used to finish is the same as they normally use.
Increasing surface strength while extending the service life is the goal of each method. Removing the weak, friable material by exposing a hard substrate and using the chemical hardening process makes it ideal for high-traffic areas.
The aesthetic appeal will also be enhanced. The floor will look clean, and crisp with a higher gloss level. This clean look works well in many designs. Industrial, commercial, and even residential projects can take advantage of any of these methods.
Maintaining a floor with a hard, smooth surface with a minimal absorption level is ideal for high-traffic areas. Contamination will be easily removed. If stain-causing liquids are removed shortly after they contact the floor, the chance of them causing damage will be dramatically reduced.
When selecting a method to increase service life, enhance maintenance, and reduce the overall cost of the floor, a burnished/polished concrete floor can be a very cost-effective method. If the floor shows abnormal staining or wear, they can be repaired. The repair process is much less expensive and intrusive than repairing any other flooring system.
Best Practices for Maintaining Burnishing Concrete Floors
No matter which method has been chosen to burnish the floor, they will need some level of maintenance. When “daily” maintenance is performed more often, it lessens the possibility of needing a more aggressive process in the future. Maintaining the floor regularly will remove unwanted incompressible materials that will ground into the surface, eating away the top surface, and lowering the gloss.
There are 3 levels of maintenance available to keep a burnished concrete floor in “as new” condition. They each have their own reason to be used.
Daily Maintenance involves regular sweeping with a dry micro-fiber dust mop removing incompressible material that will damage the floor when driven or walked on. DiamaPro® Diama-Clean, a neutral pH cleaner, may also be used when soils or stains are difficult to remove using a dry process.
- Auto-scrubber (wet)
- DiamaPro® Diama-Clean added to the freshwater tank
- Auto-scrubber fitted with a DiamaPro® Sparkle Pad – 3500-grit.
- DiamaPro® 27” High-speed Burnisher (dry)
- DiamaPro® Sparkle Pad – 3500-grit
Restore Maintenance is used when the polished floor shows traffic patterns due to heavy foot or vehicle traffic. Restore Level should be used when the floor is not responding to Daily Maintenance. The floor appears to have lost its gloss, and the floor has been stained. Perform this level until the gloss level needed has been restored and then move back to
Daily Maintenance.
- Auto-scrubber
- Must be performed wet.
- DiamaPro® Sparkle Pad – 800-grit
- DiamaPro® Sparkle Pad – 1800-grit
- DiamaPro® Sparkle Pad – 3500-grit
- Apply DiamaPro® Diama-Guard HG
- High-speed burnish using a DiamaPro® Sparkle Pad – 3500-grit dry.
Refurbish
The Refurbish Level is a process of refining an etched surface bringing it back to its original appearance. The process will take multiple steps to complete. It can be performed over a large area or to address small etched areas. No matter the size, the process needs to gradually feather into the polished area, creating a seamless repair.
- Must be performed wet with an auto-scrubber.
- DiamaPro® Sparkle Pad – 200-grit
- DiamaPro® Sparkle Pad – 400-grit
- DiamaPro® Sparkle Pad – 800-grit
- DiamaPro® Sparkle Pad – 1800-grit
- DiamaPro® Sparkle Pad – 3500-grit
- Apply DiamaPro® Diama-Guard HG
- High-speed burnish using a DiamaPro® Sparkle Pad – 3500-grit dry.
Applications for Burnished Concrete Floors
A burnished surface is an exceptionally durable flooring system that can be used in many environments. When evaluating a flooring system, the attributes of burnished concrete could coincide with the needs of the facility.
Retail
- A retail space will see an elevated level of foot traffic. A retail store floor within an enclosed mall will see much less abrasive action than one with an outside entrance. Incompressible dirt will be brought in from the parking lot and ground into the floor.
- Appearance will also be important within a retail space. The floor is usually subtle and not the main attraction. The facility wants the items for sale to stand out and not the floor. They want to minimalize the floor, set it in the background, emphasizing the items for sale. A burnished floor has a modern, soft color with a gloss level that can be matte or high gloss.
Warehousing
- Most abrasion in a warehouse is the result of continually running over the floor driving incompressible materials into the floor. Many times, there will be 50, 100, or even 200 forklifts continually moving heavy pallets over the same area in the facility. Abrasion resistance is a critical performance feature that will increase the service life of the floor.
Office Building
- When selecting a flooring system for a commercial office building, appearance could be high on the list. The interiors of such facilities are usually designed by an Interior Designer. They will be interested in durability, but the floor’s appearance needs to meld into the overall design.
- A burnished concrete floor not only has a level of gloss giving a clean, crisp look, it can also have color added to it. If a color is to be added, the polishing process will be the most likely burnishing choice. During the process, a colored, liquid dye is applied to the floor. The final polishing step locks the dye into the floor producing a translucent colored floor.
Low Maintenance Solutions
- A burnished floor has a smooth, tight, low absorption rate surface. Liquids will have a tough time penetrating and leaving a stain behind. The ultra-smooth surface will not hold onto dirt. This smooth, tight surface will be easier to clean than a conventional finished concrete floor.
When to Consider Professional Help
If there are no special repair needs, one of the burnishing processes could be a DIY project.
We supply all the tools to perform the work. If running a propane-powered high-speed burnisher is not for you, then you should contact an experienced installer.
With all tasks, experience is extremely valuable. Knowing what to do when will lead to a successful project. Unless the concrete floor is new, there will be repairs to contend with. Repairs might consist of filling control joints with a fast-setting polyurea joint filler such as DiamaPro® Diama-Joint Fill. This will entail running a diamond blade fitted to a concrete saw down the joint cleaning each side of the joint. Once the joint is clean of any bond-inhibiting debris, the joint is filled with the DiamaPro® Diama-Joint Fill.
Spalls and pinholes might also need to be filled. DiamaPro® Diama-Grout is a great material to do just that. A fast setting, polyurethane resin can be tinted to almost any color. Contractors will match it to the aggregate color or to the cement paste. By grouting a slab, the final gloss level will be enhanced.
Conclusion
There are different methods to burnish a concrete floor. Each method will develop a durable floor. The most extreme durability comes from the polishing process. At times polishing might not be within the budget. That’s why other methods can be used. If you are interested in increasing abrasion resistance or elevating the gloss level leaving the floor with a clean, crisp appearance, burnishing will be a wonderful choice.
DiamaPro Systems has everything needed to install each of the three burnishing methods. Reach out to one of our Field Representatives for guidance on which method will work best in your facility.