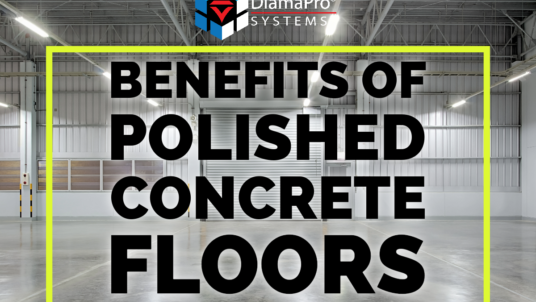
Polished concrete floors have emerged as a popular choice in industrial, commercial, and residential settings, offering a combination of aesthetics, durability, and sustainability. This article delves into the world of polished concrete floors, unveiling the multitude of benefits polished concrete brings to interior spaces. Whether you're considering these floors for your next project or simply intrigued by their allure, this guide will highlight the advantages that make polished concrete a shining star in flooring solutions.
Sleek Aesthetics and Visual Appeal:
Using polished concrete as a flooring option in your project opens a wide variety of architectural designs. By going with a highly reflective finish, the space will look large and expansive. It will have a modern feel while reflecting the available ambient light. Moving to a softer look using a semi-gloss to a matte finish, the area will have a warmer feel. Just by changing the gloss level, the entire area can change.
When polishing concrete, you remove the weakest part of the surface to enhance the long-term durability and bring out the natural beauty of the slab. During the construction phase of the project, the extreme top surface has been subjected to the environment, abrasion, and foot/wheel traffic. To successfully polish a concrete floor, less than 1/16” of the surface needs to be removed if the floor is flat and has been finished well when the concrete was placed.
Durability and Longevity:
Conventional concrete has exceptional compressive strength with a lower abrasion resistance. It can handle high loads without crushing but shows traffic patterns in high-wear areas. For an interior floor, compressive strength is usually not a concern, but abrasion resistance is.
A properly polished concrete surface is extremely abrasion-resistant with some water-repellent properties. A non-polished surface contains peaks and valleys. As the surface wears, the peaks wear down to the level of the valleys leaving visual traffic patterns. With a polished surface, there are no peaks and valleys. The entire smooth polished surface shows minimal to no wear, leaving virtually no traffic pattern.
A chemical hardener is used during the polishing process. This hardener chemically reacts with the hardened concrete to increase its abrasion resistance. With the use of a chemical hardener and having such a smooth surface when polished, the service life of the polished floor is greatly increased over a non-polished floor.
Low Maintenance Routine:
When evaluating floor systems, maintenance always needs to be discussed. How easy is it to clean and how long will it remain easy to clean? With polished concrete, there are options available for many scenarios. Warehouse, industrial, commercial, restaurant, and residential all require a process that matches the environment. Although polished concrete has a lower maintenance cost than other flooring options, just by stopping at a 400-grit diamond tool (matte) you can lower your maintenance cost even more. It takes less effort to maintain a 400-grit polish than a 1500-grit (high gloss) polish if the goal is to retain the high gloss appearance.
A warehouse will have forklifts, human traffic, and forklift charging areas. When it comes to durability, the level of polish can be matte to high-gloss. They will all perform well although the cleaning regimen will be a bit different. High gloss floors will require more attention than a matte finish to retain the higher gloss level. If a shiny floor is important, that will take more maintenance, which must be understood.
After the floor has been polished to the level (gloss) you wish, there are protective sealers that can be applied to minimize staining, water/liquid penetration, and make it easier to clean. In a restaurant, you will have food dropped onto the floor. There might be grease or stain-producing materials left behind after a quick clean-up. Selecting a protective sealer that extends the dwell time of the contaminate will help maintain the appearance of the floor.
Sustainability and Environmental Friendliness:
Working with an existing concrete floor, you can polish it and not cover it up with a manmade material. Polished concrete is environmentally friendly. You are working with what you currently have and not producing another material to cover it up, which helps the environment.
Improved Indoor Air Quality:
Once the floor has been polished, the finished system does not emit any harmful toxins into the environment like some other flooring systems. You are polishing what is already in place and not installing a new floor system.
There are chemical hardeners that can be used in the polished concrete process that contain anti-microbial technologies reducing the growth of fungal and bacterial microbes. They will not alter the polishing process, only enhance the protection from harmful microbes. This type of material needs to be specified. Not all manufacturers utilize this technology, but DiamaPro Systems has a line of chemicals with Microban® Antimicrobial Product Protection that are the perfect choice for any facility that prioritizes sanitation.
Cost-Effectiveness:
When comparing the cost of polished concrete to other floor systems such as carpet or VCT, the initial installation is lower, the maintenance cost is lower, and the life cycle is longer.
When installing VCT many times the floor will need to be ground or floated with a cement based leveling material to remove, cover or fill imperfections. These imperfections will mirror through the VCT producing high ridges in the surface. These ridges are not only unsightly, but they provide a high area to wear faster than the flat portion of the tile.
Moisture is another factor that needs to be addressed. With polished concrete, moisture vapor is allowed to pass through like a conventional slab, without an issue. VCT and carpet have no such luck. After the slab has been ground and flattened, a system needs to be applied to address moisture vapor transmission (MVT). MVT is an issue with floor systems that might not breathe well enough allowing the vapor to escape. If the moisture vapor is trapped between the concrete substrate and the flooring system, it can cause bubbling, delamination of the flooring system, and possible microbe growth.
Once the floor is ground flat or floated, a moisture mitigation system installed, and the floor system installed, polishing the slab has a lower cost without even mentioning the maintenance.
Maintaining VCT is simple, but high cost. The floor needs to be waxed on a regular basis based on the environment. After several waxings, the floor needs to be stripped removing excess wax that has not been worn away. After that, the waxing regimen needs to start all over again. Carpet is similar. If not vacuumed daily and shampooed periodically, the dirt in the carpet will break the fibers down and the carpet will need to be replaced.
Life Cycle:
The expected lifespan of VCT is 8-10 years. Carpet, depending on the type and environment, has a lifespan of 5-15 years. Polished concrete will never wear out to the point where it needs to be replaced. Polished concrete can go through a revitalizing process that is much less intrusive than the initial installation to bring it back to new.
Versatile Design Options:
Another of the great advantages of polished concrete floors is their versatility. When designing with polished concrete you can include texture, color, exposure of large aggregate, or show only fine sand. The same gloss level can be specified over the entire floor or have multiple gloss levels on the same floor.
Conclusion:
Polished concrete floors go beyond being a surface to walk on – they represent a harmonious blend of style, practicality, and eco-consciousness. With their unmatched durability, sleek aesthetics, and environmental advantages, they stand as a compelling choice for modern interiors. Whether you're seeking a flooring solution that balances elegance with longevity or a sustainable option that adds value to your space, polished concrete floors shine in every aspect.
If you are looking into the benefits of polished concrete floors, reach out to DiamaPro Systems for more information on necessary equipment, tools, chemicals, and more!