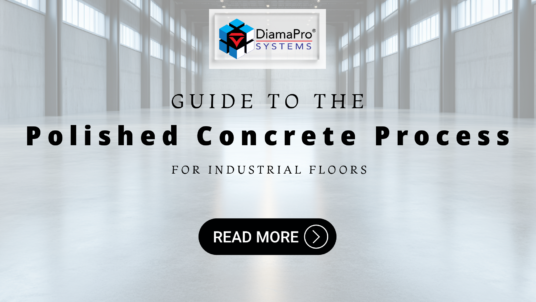
In the beginning, metal bond diamonds were the primary tooling used when cleaning the floor. Metal bond tooling was the most aggressive at the time. Their primary use was to remove surface contaminates and the top surface of a concrete slab. A metal alloy encapsulates the industrial diamond abrasive. The alloy is produced in multiple hardnesses. The hardness of the metal used correlates to the hardness of the concrete.
The hardness of the concrete is found using the MOHS Hardness Test. This test decides the hardness value of the concrete surface to enable the proper choice of metal bond tooling. Hard alloy is used for soft concrete and soft alloy on hard concrete for greater tooling life and production rates.
As the development of tooling progressed, the surface was not only ground but also honed and polished producing a durable, attractive floor without a topical coating. It is known that removing the weak, friable surface, inducing chemical hardeners, and polishing the surface produces a hard, abrasion-resistant wear surface, perfect for areas in an industrial facility.
By understanding the equipment, the process, and the potential benefits it can reap a polished floor is a low-cost solution to be used where high, abrasive traffic takes place. Polished concrete started in factories but since then, they have been installed in commercial, hospitality, grocery, and residential buildings. It is not only durable but also architecturally pleasing.
What Are Polished Concrete Floors?
A polished concrete floor is when using different grit industrial diamonds to “sand” the surface. Starting with a coarse tool and gradually working up to a fine grit. This process produces a hard, durable, reflective surface that works in a variety of environments.
There are added benefits to a polished surface. The abrasion resistance increases when the weak surface is not only removed but chemically treated, increasing the hardness of the cement paste.
Because the surface is smooth, dirt and other contaminates will not grab onto it. The maintenance of a polished surface is quite simple when using the proper equipment and cleaning chemicals.
The industrial look is becoming a modern design feature used more often in commercial workspaces. With an industrial plant, it fits right in without the use of a pigmented coating that could scratch or peel. The polished surface will also reflect light increasing the ability to enhance the brightness in an area. If a softer appearance is desired, a less reflective, matte finish is available.
With the flexibility of the polishing process, different looks are produced with the right substrate. If the slab is in good condition, you can get both sand and coarse aggregate exposure. If there is a considerable amount of rough concrete to remove, only a coarse aggregate exposure is possible. No matter which one is selected, durability will not change much.
Over the past years, there has been an influx of projects specifying polished concrete. Restaurants, grocery stores, office complexes, and even residential homes are seeing polished concrete used as a floor system. If there is a concrete floor, polishing it is a workable possibility. Industrial facilities and warehousing will always be the number one user because of the benefits it offers.
Essential Tools & Materials for Concrete Polishing
Polishing a concrete slab is like sanding wood. Start off with an aggressive abrasive removing large imperfections and move on to finer and finer grits until there are no visible scratches and a gloss is produced. The top layer of the slab is a weak, friable material that normally shows wear from traffic. The first grinding step will uncover a sand or aggregate layer depending on how much has been removed. At that point, this will be the level of aggregate exposure you will see. The final appearance will be developed within the polishing steps. High, medium, or low gloss will be the options.
The main piece of equipment will be the grinder. The grinder is fitted with the diamond tooling according to the step being performed. There are two styles of grinders, planetary and rotary. Both will do the job so it’s personal preference on which to use. They do have their own specialties though.
Rotary grinders are typically beefier. Its high low-end torque is well suited for tough grinding projects without being overstressed. Removing thick or rubber-like coating systems or grinding with an extremely aggressive tool is where it excels. You can polish with them; they will produce nice floors, but it takes a bit more experience to run.
Planetary grinders are more of a finesse-type machine. Don’t take me wrong, it can be used to remove tough coatings, but it excels in the polishing world. The grinding or polishing action of the grinder's heads lends itself to producing a flat, well-processed surface.
Anytime concrete dust is generated, an industrial HEPA dust extractor (vac) needs to be attached to the machine. Depending on the grinder size, the proper vacuum might have 2 or 3 motors and power requirements of 110v or 220v. As dust is drawn into the vac, the heavy particles fall to the bottom where a tube-style bag system is attached. The air then travels through a main filter. This filter captures the majority of remaining dust but will clog over time. On a regular basis, this filter needs to be purged. The purging process shakes the dust free from the filter material falling to the bottom and then into the bag system. Once through the primary filter, the air is sent to the HEPA for final cleaning.
The grinder provides power, and the tooling provides cutting. Except for unique-use tooling, industrial diamonds are the abrasives that do the work. The industrial diamond is encapsulated in either a metal alloy, ceramic, or resin material. Typically, the finer the abrasive grit, the softer the bonding material.
Metal bonds are for grinding, transitional or ceramic bonds are for honing, and resin bonds are for polishing. The finer the diamond grit, the softer the bonding material. This allows it to wear away easily, exposing fresh diamonds when polishing a smooth surface.
Densifiers react with a byproduct produced during the concrete hydration process producing more glue, binding everything into a solid mass. This improvement provides a harder surface. A hard, concrete surface is better when polishing to a higher gloss. A hard, solid surface will also have an extended service life over a non-treated surface. High abrasion resistance will keep the overall appearance, which is a great benefit to the client.
Industrial floors will get dirty. Forklifts, foot traffic, and the manufacturing process taking place produce and track dirt. General housekeeping consists of daily cleaning and removing dirt and grime. The combination of an auto-scrubber fitted with a diamond-impregnated pad works well. If a cleaner, such as DiamaPro® Diama-Clean 30, is added to the freshwater tank, the cleaning process will be much easier and more efficient.
To make maintenance even easier, a sealer is applied. DiamaPro® Diama-Guard is a sealer for polished concrete that develops a thin protective film reducing the negative impact from assorted contamination. In an industrial facility, it can be considered sacrificial due to the high traffic levels. On a semi-regular basis, Diama-Guard can be reapplied after a deep cleaning. Large grinders are not necessary to perform this work. All that is needed is an auto-scrubber fitted with a diamond-impregnated pad and Diama-Clean 30 for surface preparation. The method of application of Diama-Guard is the same as the first installation.
Step-by-Step Polished Concrete Process
The condition of the concrete slab will dictate which abrasive you will start with. Is there a hard or soft concrete surface? Is there a topical coating currently on the slab that needs to be removed? All these scenarios have a bearing on tooling choice.
Preparation
- Defects need to be taken care of before starting the grinding process. The defect will lead you to the proper repair material. Spalls are usually medium size chunks removed in the surface.
- Cement-based materials work well to repair these areas, but the cure time can be long.
- Resinous repair materials cure fast, allowing the grinding process to begin. DiamaPro® Diama-Grout, a flowable urethane resin, is a material that can be mixed with dry sand, cement, or cement-based overlay material, producing a repair mortar for deep repairs.
- Cracks, chips, and pinholes might be uncovered after the first grind. Diama-Grout neat, without dry filler, can be thinly troweled over the entire floor filling these imperfections. This is performed after the first metal bond cut.
Grinding
- Start grinding with a tool that will produce the desired aggregate exposure or one that will clean the concrete surface removing imperfections.
- When moving to a finer grit, double the earlier grit. If starting at a 30-grit, the next step will be a 60-70grit.
- Making the move from a metal to a resin tool for polishing, a transitional is used. Transitional tools are produced in 50, 100, and 120-grits.
- The polishing steps are performed with a resin bond tool. This is the step where the gloss is developed.
- · Example: Metals – 30, 70
- Transitional – 50, 100
- Resins – 100, 200, 400, 800
- · If there is an existing coating that needs to be removed, A polycrystalline diamond (PCD) will be used. PCDs are extremely aggressive and have a segment shape that will sheer the coating from the floor, unlike a normal diamond tool. A normal tool does not have the ability to cut into the coating. It will slide over the top of it. Once the coating has been removed with a PCD, move to a 30-grit metal to clean the floor.
Densifying
- Concrete is hard to touch but there are different degrees of hardness. Using the MOHS Hardness Test the actual hardness can be found. When polishing it is good to have a hard, concrete surface. It will also help the client by increasing the abrasion resistance and extending the service life.
- During the hydration process, concrete paste goes through a transformation. It starts with water and powdered cement. When combined, they produce a chemical reaction. Two main chemicals develop in the reaction, calcium silicate hydrate (CSH), and calcium hydroxide (Ca(OH)2). CSH is the glue that binds the sand and aggregate. Ca(OH)2 is a byproduct of the reaction that is not needed. Densifiers react with Ca(OH)2 producing more CSH. This will increase the hardness and long-term durability of a concrete surface.
- Densifiers are applied during the polishing process. They have a surfactant that increases their ability to absorb into a tight surface. After the 200-grit resin cut, the densifier is applied to the point of rejection. This process will increase the hardness of the concrete surface.
Color
- If a color is desired, one can be applied. Dyes are colored solutions that penetrate well into the substrate.
- Once the carrier (liquid) has evaporated, the dyed particles attach to the slab providing color.
- This coloring method is applied between 100 and 200 resin steps.
Sealer
- Vacuum the area by removing all dust.
- With an auto-scrubber fitted with a diamond-impregnated pad, wash the area.
- Allow to dry.
- Using a low-pressure pump sprayer, apply a thin, even coat of DiamaPro® Diama-Guard.
- Right behind the application, evenly spread while leaving no mop marks, with a microfiber pad.
- Allow to dry 2-4 hours.
- Apply a second coat in the same manner as the first.
- Allow to dry.
- Burnish with a high-speed burnisher and 3500 grit Sparkle Pad.
Maintenance & Care for Polished Concrete Floors
The goal with any floor is to keep the original appearance and performance. With polished concrete, it is easy to tell if it has been properly taken care of. The first thing that changes is the gloss level. If the gloss is diminished, it’s time to step up the maintenance program.
Three levels of maintenance are used at various times, Daily, Restore, and Refurbish.
Daily Maintenance
- As a daily process, this will help keep the gloss and remove any light stains that impact the final appearance.
- This process should be performed daily.
- Auto-scrubber fitted with a 3500-grit DiamaPro Sparkle Pad and DiamaPro® Diama-Clean 30
Restore
- Periodically, the polished floor will show traffic patterns due to heavy foot or vehicle traffic.
- Refurbish Level should be used when the floor is not responding to Daily Maintenance.
- The floor appears to have lost its gloss and stains have appeared.
- Perform this level until the gloss level has been restored and then move back to Daily Maintenance.
- Restore Process
- Auto-scrubber fitted with a DiamaPro® Sparkle Pad and DiamaPro® Diama-Clean 30
- DiamaPro® Sparkle Pad – 800-grit
- DiamaPro® Sparkle Pad – 1800-grit
- DiamaPro® Sparkle Pad – 3500-grit
- Apply DiamaPro® Diama-Guard HG
- High-speed burnish using a DiamaPro® Sparkle Pad – 3500-grit dry.
Refurbish
- The Refurbish Level is a process to refine the etched surface to bring it back the its original appearance.
- The process will take more than one step to complete.
- This can be performed over a large area or to address small etched areas.
- The process needs to gradually feather into the polished area, creating a seamless repair.
- Refurbish Process
- Auto-scrubber fitted with a DiamaPro® Sparkle Pad and DiamaPro® Diama-Clean 30
- DiamaPro® Sparkle Pad – 200-grit
- DiamaPro® Sparkle Pad – 400-grit
- DiamaPro® Sparkle Pad – 800-grit
- DiamaPro® Sparkle Pad – 1800-grit
- DiamaPro® Sparkle Pad – 3500-grit
- Apply DiamaPro® Diama-Guard HG
- High-speed burnish using a DiamaPro® Sparkle Pad – 3500-grit dry.
When looking at preventive maintenance, remove stain-producing materials as soon as possible. The longer they dwell on the surface, the greater the chance of staining. Dirt and sandy materials should also be swept up. Everything will scratch if an abrasive is harshly ground into it.
Walk-off mats at entrances to the building trap abrasive particles that can negatively impact a polished floor. Shoes will also be wiped clean of tar and oils.
Conclusion
When polishing a floor, there are things to consider, such as the condition of the concrete surface, the grinder, the tooling selected to produce the desired finish, and how to maintain the original appearance. Developing a work plan will help prepare you for a successful project.
DiamaPro Systems offers a variety of grinders, tooling, and chemicals specifically suited for the polished concrete industry. Our trained field representatives will guide you through the process.