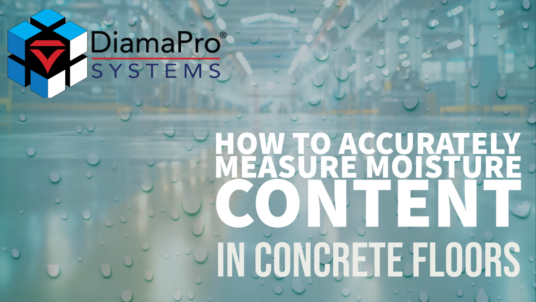
Moisture content and moisture vapor transmission can be measured providing a numerical value for each. When applying a coating to a concrete slab, moisture could impact its performance. Bubbling and bond failure are two of the crucial issues.
Standard test methods are used to find moisture content and moisture conditions within a concrete slab. Each test is suited for a different task and has varying levels of accuracy and efficiency.
If the moisture within the concrete is not allowed to equalize with surrounding conditions before a coating or flooring product is applied, it can accumulate below the flooring or coating, causing discoloration, cupping, buckling, blistering, adhesive failure, and mold growth, leading to potentially costly repairs.
Why Measuring Moisture in Concrete is Essential
Moisture within the slab or at the surface will affect floor-covering materials. If the flooring system has minimal breathability, moisture will build at the bond line causing a bond failure. Some systems do not cure well in the presence of moisture. It interferes with the chemical reaction that develops the ultimate strengths.
Some systems require a primer to be installed before the actual floor covering. The premise of the primer is to seal the surface enhancing the bond strength. Primers can also be moisture vapor barriers. They lock the vapor in the slab reducing the probability of having an issue.
Moisture issues are not only isolated to new concrete slabs. When new, a physical vapor barrier is normally installed before the placement of the concrete. This blocks ground moisture that will travel through the concrete to the surface affecting flooring materials. With old slabs, it is difficult to find if there is a vapor barrier or if it is intact. That’s when a surface-applied vapor barrier is needed.
DiamaPro® Moisture Control is a topically applied moisture control material that controls the amount of moisture vapor leaving the slab. It also has Microban®, an anti-microbial additive. Microban® drastically reduces mold and mildew from growing if moisture accumulates under the floor covering. This system works well for most flooring systems, but the floor system manufacturer might have a specific moisture vapor system that they recommend. Always check with the manufacturer when deciding suitability.
Concrete moisture content, %RH (relative humidity), and MVER (moisture vapor emission rate) are all measurements that can help indicate the moisture condition within a concrete slab. Often, the goal is to determine if the slab is ready for a flooring system to be installed. If readings are not taken, or not taken accurately before installation, a critical flooring system failure is possible.
Methods to Measure Moisture Content in Concrete
There are various methods used for concrete moisture measurement. The two most common methods used are non-destructive electronic impedance (resistance) meters and in situ relative humidity (RH) probes.
Non-Destructive Concrete Moisture Meters
Non-destructive concrete moisture meters (electronic resistance meters) measure concrete moisture using the principle of electrical resistance of concrete, which is related to concrete moisture. An alternating electric field flows from the device’s transmitting sensor pins through the substrate and is captured by the receiving electrodes. Resistance is measured with increasing concrete moisture causing an increase in the resistance reading. Using concrete standards with known moisture levels, the meter can be calibrated to read in units of concrete moisture.
Concrete moisture meters provide an instant result, without the need to drill into the concrete, completely non-destructive. However, impedance can also be affected by changes in concrete composition or the presence of rebar within proximity to the surface. So, the test is less accurate than invasive (destructive) options. These meters measure the moisture near the surface of the concrete, so high moisture levels near the center or bottom of the slab may go undetected. ASTM F2659 recommends non-destructive concrete moisture meters as a tool to find areas of relatively high moisture within the slab, very quickly and at a low cost.
In Situ Concrete Relative Humidity Probes
In situ concrete relative humidity probes, as described in the ASTM F2170 standard test method, are highly accurate for measuring moisture in concrete. This procedure involves drilling a hole into the concrete slab (typically 40% of the total thickness of the slab) and then using an electronic relative humidity probe to measure the moisture within the slab.
Since they directly measure moisture/humidity levels near the center of the slab, they provide a quantitative measurement that is used to determine when a slab is ready for the application of coatings or flooring products. Drilling a ¾” wide hole within the concrete is needed, in addition to waiting 24 hours to have the area in and around the hole come to equilibrium.
Other methods for Measuring Concrete Moisture
There are other less popular or older methods for deciding the moisture content within a concrete slab, such as the calcium chloride method (ASTM F1869) and the plastic sheet method (ASTM D4263).
Anhydrous Calcium Chloride Moisture Tests
Anhydrous Calcium Chloride Moisture Tests involve measuring the increase in weight of calcium chloride as it collects moisture from an encapsulated area on the concrete surface. A greater increase in weight shows greater levels of moisture in the concrete.
Calcium Chloride Tests are inexpensive and relatively simple to use. However, they only measure moisture at the near-surface or exiting the substrate. There is a waiting period before results are available, typically 24 hours. There is no practical way to calibrate these kits, and they can be heavily influenced by ambient conditions.
Step-by-Step Guide to Measuring Moisture in Concrete Floors
Depending on the test method or instrument used, different depths of the concrete slab can be measured. The following description describes the difference between the three most popular test methods, anhydrous calcium chloride moisture tests, in situ relative humidity (RH) probes, and electrical impedance (resistance) concrete moisture meters.
Anhydrous Calcium Chloride Moisture Test - as described by ASTM F1869, measure MVER from the surface of the concrete slab, usually the top ½–¾ inch of the sample being measured.
- In one or more areas, clean a 2.00’x2.00’ square of the slab.
- Remove all sealer and moisture-blocking materials.
- Set the open container of calcium chloride in the middle of the clean area.
- Adhere the plastic dome, which comes with the kit, over the dish of calcium chloride.
- Allow it to sit, undisturbed, to absorb the airborne moisture vapor captured in the dome.
- After 18-24 hours remove the dish and put the cover on.
- Weigh the dish and use the calculation to figure out the vapor value.
- The test value is expressed in lbs. of vapor leaving the slab over 24 hours in a 1,000 sqft. area.
In Situ Relative Humidity Probe - as described in ASTM F2170, measure at 40% depth of a concrete slab that is being dried on one side (top or slab on grade) or 20% depth of a concrete slab that is drying from two sides (top and bottom). If the slab is 6 inches thick and dried on one side. 40% of 6 inches is 2.4 inches. That is where your RH values will come from.
- Drill a hole as described in the kit.
- Dry clean the hole well.
- Allow to set for a minimum of 24 hours allowing the moisture to equalize. The drilling process creates heat and dries out the hole. Once cooled to slab temperature, the moisture will equalize.
- Insert a probe or meter into the hole.
- Let it sit for 24 hours.
- Take the reading.
- The value will be in a percentage ranging from 40%-100%.
- Floor covering manufacturers will publish their maximum value.
Non-Destructive Electrical Impedance Concrete Moisture Meter - as described in ASTM F2659, generally measures moisture content down to ¾–1 inch from the top of the concrete slab. There are moisture meters that can provide humidity value and an electrical impedance value. Electrical impedance testing is non-destructive, and the reading is immediate. Readings can be taken throughout the floor and one after another. The unit is portable and hand-held. When owning the meter, an unlimited number of tests can be taken for the price of a battery.
- In a 1.00’x1.00’ area remove all sealers and curing compounds. Do not use water.
- Turn the meter on.
- Set on a clean surface.
- Activate the meter and take the reading.
- The value will register as a percentage typically ranging from 3.00% to 9.00%.
- Floor covering manufacturers will publish their maximum value.
Best Practices for Accurate Moisture Measurement
First, follow the test method recommended by the floor covering manufacturer. Manufacturers will publish the method and maximum value the system has been built around.
When performing the test, selecting multiple test sites will provide the most reliable information. Contractors use the Non-Destructive Electrical Impedance Concrete Moisture Meter to figure out if a surface problem occurs. If the numbers are low, there is a good chance the other methods will show the same. If the numbers are high, relative humidity tests should be performed.
Electrical Impedance and Anhydrous Calcium Chloride Moisture Tests are both a snapshot of the moisture vapor condition at the time of the test. Moisture vapor will always move from warm to cold. If your floor is warmer than the air, the moisture vapor in the concrete will leave the slab. If the air is warmer than the slab, moisture vapor will move into the slab. This phenomenon can happen quickly and change throughout the day. A test run today could produce different results than one run last week.
In Situ Relative Humidity Probe test measures relative humidity within the slab. Once the floor is in a stable, climate-controlled environment, the moisture level will remain stable throughout the slab. This reliable test method finds if you will have a problem in the future. This test is usually performed by a registered engineering firm.
Addressing High Moisture Levels
When installing a floor covering that has minimal to no breathability on a substrate with elevated moisture levels, a moisture barrier or moisture control agent needs to be used.
Moisture surface barriers dramatically slow down the movement of moisture vapor through the topical system. It is a film-forming system that when applied correctly, can be used under many flooring systems. They can hold back as much as 20 lbs./1000 sqft/24 hours.
Moisture control systems, like DiamaPro® Moisture Control, control the rate the vapor passes through the concrete surface minimizing the detrimental effect the vapor can have on a non-breathable coating system. It is a non-film forming system that once it has fully penetrated and dried, will not alter the appearance of the substrate and most flooring systems will bond to it.
One other way to react to elevated levels of moisture is to wait until the values are lower on their own and are acceptable. Now, this might take days or months. If time is of the essence, selecting another method is your only choice. Some professionals specialize in moisture vapor transmission. They have a good understanding of which test method will be best for your project.
Conclusion
In concrete, moisture is seen in two forms: liquid and vapor. Concrete is like a sponge; it can absorb a tremendous amount of water once cured. This water can come from one or multiple sources. When concrete is produced, more water is used to increase its workability, and it takes time before it leaves the slab. Concrete placed on grade (on the ground) can absorb moisture from the ground. This can be a short-term event or continue for years. Water can also enter the concrete from the top surface.
Flooring systems have a specific moisture level that can be tolerated before a failure appears. By knowing the moisture range that is acceptable for the system, you will be on your way to installing a successful project.
DiamaPro® Systems can offer valuable advice through their distribution channels. Niagara Machine, DiamaPro’s Master Distributor, has a sales force that is deeply knowledgeable. They visit job sites daily helping contractors by providing advice on a multitude of concrete-related issues. Give them a call and minimize potential issues.