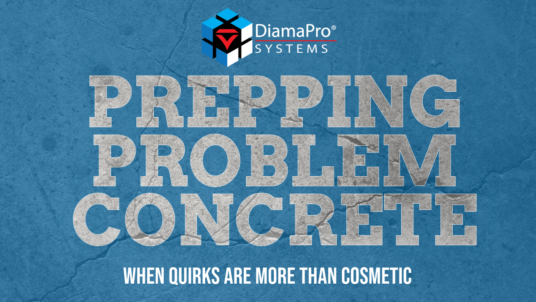
There might be defects discovered during the slab assessment. Most defects are repairable, but not all. Some repairs might be acceptable for one flooring system but not for another. At that point, a decision will need to be made. Can the specified system be installed, or will a change order need to be given, including a variation or a completely different flooring system?
Moisture
Concrete is sponge-like. It will easily absorb and let go of moisture. If there is a source of moisture and the ambient conditions are right (or wrong), an interior slab will have moisture in a vapor form in and out regularly.
During the slab evaluation process, the moisture vapor transmission (MVT) level should be found. During the construction phase, a moisture barrier can be installed on-grade before the reinforcing steel. This will reduce the free moisture that emits from the ground adversely affecting the flooring system.
Most material manufacturers will publish the maximum MVT allowable for the system selected. A moisture barrier can be applied directly to the slab before the system is installed mitigating a vapor issue. After the moisture mitigation and floor systems are installed, the floor system will appear as if it were installed on bare concrete.
There will only be a performance change and not a visual one.
If the flooring system is clear, DiamaPro® Moisture Control can be used. Moisture Control controls the rate of the vapor emitted from the floor below the surface. Once applied and dry, it is undetectable. Any system can be used over it without visually affecting the final appearance of the floor system.
Crack Types
There are two types of cracking, dynamic, and static. Dynamic cracks will continue to open and close over the life of the slab. Static cracks will only move once at the time the crack happened.
Dynamic cracks continually open and close. They are acting the same as a moving joint. Typically, they occur when there is not a joint placed in an area where one should be, and the concrete slab made its own.
Static cracks are considered nonmoving. They happen due to an impact or overloading situation. If something extremely large falls on the slab and cracks appear, these will not move again. When a heavy vehicle rolls on a slab that is not designed to manage such load, static cracks might appear.
To figure out the type of crack, a crack monitor can be used. This device is placed over a crack, adhering it on each side with an epoxy adhesive. As the crack moves, the monitor slides back and forth over the crack showing the amount of movement.
Dynamic Cracks: These cannot be effectively repaired. Once filled or glued back together and it moves again, a crack will reappear in the same place or right next to it. These are to be sealed with a flexible joint sealant. This will allow for future movement while keeping water or dirt from entering the void.
Static Cracks: These can be glued back together by gravity feeding and pressure injecting a structural resin into the void. If these do open or develop a crack next to the crack, treat them as a dynamic crack.
DiamaPro® Diama-Grout is a gravity-fed material. It is a two-component system that is packaged in 2-gallon bulk units and 600 mil side-by-side cartridges with a static mixing nozzle. It is low viscosity and will penetrate fine cracks. It is not a structural repair. It has flex allowing for slight crack movement, but it should not be used in a dynamic crack.
In the pressure injection market, there is a theory to treat all cracks as being static unless there is a definite sign of movement with the understanding that they might open.
Adequate load Barring Capacity
If the project is a change of use, decide if the structure can support what the new use will be. If the slab is on grade (dirt below) and heavily cracked, was there enough concrete mass to support the weight? A 3,000-psi concrete at 4.00” thick slab will support more weight than 3,000-psi concrete at 3.00” thick.
Concrete has high compressive strength and can manage heavy loads. Very seldom you will observe a concrete floor crush due to a consistent, heavy load. Cracking could occur if there was a void under the slab. To perform as intended, the slab needs to be in full contact with a well-compacted subgrade. This allows the weight to transfer through the slab and into the subgrade.
If there is a void between the subgrade and the concrete slab, it can be filled. Injecting a structural foam through drilled holes can be used. The foam will expand once placed to fill the void. “Mud” jacking can also be used. Like foam injection, holes are drilled into the slab. A mixture of water, cement, and admixtures, to promote flow, is pumped under the slab to fill the void.
Elevated slabs are placed on a metal pan deck which is left in place or formed and poured with the forms being removed once the concrete reaches sufficient strength. Both systems will be designed to withstand a designed dead and live load. Granted, there are ways to increase the load barring ability if needed but that can be costly. This is when a structural engineer will have to prescribe the strengthening system needed.
Exposed Corroded Reinforcing Steel
American Concrete Institute (ACI) 318 recommends 1.5” of cover over reinforcing steel for normal use. If deicing salts are used on the slab, the coverage increases to 2.00”.
Corrosion needs 3 things for it to happen. It must have an adequate amount of moisture, oxygen, and a low pH environment. If one or more are absent, corrosion will not start.
Concrete is high in pH and considered a passive environment. In this environment, corrosion will be at rest. Oxygen is almost everywhere except underwater. That is why reinforced concrete columns can last for years if they are continuously submerged. At the splash zone or water line is a different story. That is where damage from corrosion will begin once the concrete pH is lowered.
What will lower the concrete's pH? Carbonation is the reaction of carbon dioxide in the air and concrete which lowers the pH. Carbonation will penetrate the slab at a rate of 0.039 inches per year in a quality concrete mass. Once the pH drops below 9.5 at the reinforcing steel, corrosion will begin if water and oxygen are also present.
Deicing salt will also promote corrosion but not directly. Salt will accelerate the carbonation process lowering the pH of the concrete much faster than normal. This is why, in a salt-rich environment, there is a need for more concrete cover over the rebar. It will aid in increasing the time before the steel becomes corroded.
To repair corroded reinforcing steel, remove the concrete around the affected steel leaving at least a 1.00” gap around the bar. Remove all the corrosion from the steel. In a non-structural application, if 50% or greater of the diameter of the steel is damaged, a new section should be spliced in. When there is corrosion in a structural element, a structural engineer should get involved to assess the situation.
Uneven Slabs or Joint Curling
Joints are placed to provide movement in the slabs. Once the joints are placed, each side of the joint becomes separate slabs. If they are not tied together, there might be some shifting and one side rises above the other.
Slab curling can also be an issue. When the concrete is placed, in an ideal world, the slab should dry at a uniform rate. As water leaves the fresh concrete, the mass becomes smaller and shrinks. If the top of the slab dries out too fast, it will pull up the sides of the slab causing it to curl, similar looking like a potato chip. Slab curling is prevalent in fast-track projects without proper curing methods. If the concrete is cured correctly, moisture is kept in as long as possible minimizing this issue.
Curling usually happens at a joint. A scarifier can be used to even out the two sides. In doing this, coarse aggregate will be exposed. When applying a clear flooring system, this might be unsightly. The owner needs to be aware of this.
When a slab curls it could leave a void between the slab and subgrade. This void should also be filled as described above. If not filled, when heavy loads are rolled over this area, the slab could snap, producing a static crack that will need to be repaired.
Spalling
The causes and repairs of spalling can be its own article. Briefly, there are a multitude of causes for spalls. If the slab has been rained on right after placement. The cement paste is not yet strong enough and washes away exposing the aggregate. This is a surface repair. Use a repair material designed to fill the depth of the defect and follow the manufacturer's application instructions.
Joint spalling is due to impact of the joint shoulder. This can be repaired using DiamaPro® Diama-Grout filled with an oven-dried sand or aggregate. Anytime there is a spall deeper than 1.00”, always saw cut around the defect providing a definite termination of the repair. This is a safe step for all spall repairs. Technically, no repair should end on a feathered edge.
Chips and pinholes will also be common. DiamaPro® Diama-Grout can be used neat, with no sand or aggregate, to fill these. Mechanically clean the spall and overfill the defect with the Diama-Grout. With a hand grinder smooth the cured repair level to the surface.
Selecting the Right Prep Approach
With almost every floor, there will be issues. Whether cracks, spalls, or uneven slabs are the issues, how they are repaired will decide how well your finished flooring system will look and perform. Selecting repair methods based on the finished flooring system is particularly important to have a positive result.
Conclusion
The repair of defects before installing a floor system can be time-consuming. There are times when the preparation takes as long as installing the system itself. Even if it takes more time than expected, rushing or cheapening this step will only cost more later on.
The choice of the repair method is also important. Not all methods will be right for all flooring systems. Consult with the flooring systems’ manufacturer for a recommendation for your situation. No one is familiar with every repair method available. Rely on your suppliers and use their experience to your advantage.
DiamaPro Systems collaborates with owners and contractors guiding in all concrete-related matters. From surface preparation to material choice, our well-trained field personnel will be able to guide you through this process.