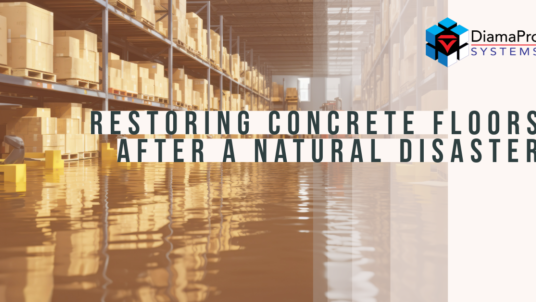
Ensuring your safety, your family’s well-being, and the health of the community, as well as rebuilding destroyed or damaged commercial or residential structures, are all aspects of post-disaster recovery. Recovering from a disaster is a complex and multi-phase process that requires coordinated efforts to ensure safety, restore essential services, and build for the future.
The phases of post-disaster recovery can be broken down into immediate actions, short-term restoration, and long-term planning. Immediately after a disaster, ensuring safety is the top priority. Individuals and local authorities must quickly secure the area and protect lives.
The Importance of Disaster Restoration
The first response phase begins once the immediate safety measures are taken care of. Survey the surrounding area for dangers such as fallen power lines, gas leaks, sharp debris, and unstable structures. Avoid entering damaged buildings until they have been declared safe.
- Conduct Damage Assessments:
- Assessments are crucial for understanding the extent of the disaster’s impact.
- Rapid Needs Assessments:
- Find immediate threats and priorities for life-saving efforts.
- Initial Damage Assessments:
- Estimate the overall damage to infrastructure.
- Long-Term Recovery Assessments:
- Collect detailed data to inform future rebuilding and recovery plans.
- Engage Local Stakeholders:
- Include community leaders, emergency responders, and long-term recovery teams to ensure all sectors are represented during assessments and planning.
Common Concrete Floor Damage Caused by Natural Disaster
Natural disasters are produced in diverse ways. They also have their own way of producing damage. Water, fire, wind, and impact are the most common and destructive. When it comes to the concrete floor, any one of these will have an impact on its appearance and service life.
Water will damage all floor coverings. Wood will warp, vinyl tile adhesive will lose bond, and carpet will absorb water and odors. In a fire, concrete will not burn, but if hot enough, the coarse aggregate having moisture will expand and rupture. This can be a violent action that will create severe concrete surface spalling. It is highly recommended that with all fire-damaged concrete, a qualified engineer should perform an in-depth evaluation. High impact will cause all types of damage and might not be able to be repaired.
Once the area has been cleaned and the concrete surface exposed, now is the time to evaluate the extent of damage. Carpet, wood, and vinyl tile can be removed. Spalls, joints, and nonstructural cracks can be filled. If the concrete slab looks to be in bad condition, a structural engineer can be called, or if it’s a slab on grade, torn out and replaced.
Equipment Used in Concrete Floor Restoration During Recovery
During the recovery effort, carpet, vinyl tile, ceramic tile, and wood floor coverings will most likely need to be removed. Hand scraping these materials can be labor intensive and at times dangerous.
The danger involved in the removal is not only physical but also the potential of mold, mildew, and fungal spores going airborne. These airborne microbes will have a negative impact when brought into your airstream. Wearing a cartridge mask designed for airborne microbe protection is necessary.
If water is involved or the concrete floor needs to be cleaned, an auto-scrubber is an efficient method to perform the work. Auto-scrubbers have two tanks, one with fresh water and one to capture the dirty, contaminated water. To ease the cleaning process, an industrial-grade floor detergent such as DiamaClean-30, can be added to the clean water tank. This will help break down the contaminate and enhance the scrubber’s ability to remove it.
Beneath the auto-scrubber is a rotating brush or pad to agitate the clean water and squeegee to extract the dirty water. Using water to initially clean the floor will reduce any airborne hazard. The dirty water can then be disposed of without you contacting it.
Air scrubbers work similarly to a forced air furnace. It draws air through a filter trapping dust and other particulates. When tearing out flooring, airborne particles will be generated. Having a simple, lightweight machine that can be moved from room to room will also be helpful. Commercial air scrubbers are available in varied sizes. They are rated as how many cubic feet of air can move through them in one minute (CFM). To decide which model will work for you, calculate the volume of the room or area you are working in. Multiply the square footage of the room by the height in feet. Example: 20’x20’ room has a square footage of 400. The room has a 10’ high ceiling. 400x10=4000. Using a 1000 CFM air scrubber, the air in that room will be cleaned every 4 minutes. The type of filter you select will depend on what you clean the air from. Large or small particulate, or a slight odor, there is a filter that will work. A transfer tube can also be attached to the exit port on the air scrubber to move the drawn-in air to the exterior of the building.
Physical hazards can be minimized, fatigue reduced, and production increased by using a commercial floor scraper when removing carpet, tile, and wood flooring. Scrapers come in varied sizes, weighing 85 lbs. to 4500 lbs. The weight, or down pressure, will have an impact on the production rate. A heavy machine will remove up to 8,000 sq.ft. of carpet per hour. The larger the machine, the more productive it will be. Weight has its drawbacks. The typical elevator will only carry 2500 lbs. so a freight elevator needs to be available. Some buildings do not have a floor system capable of carrying an abnormal amount of weight. That is why there are smaller, lighter-weight machines like the DiamaPro SCR series. They have similar performance in a smaller package built for less accessible projects.
During the clean-up process, a vacuum or dust extractor will be an extremely useful tool. There will be dry materials that will need to be removed off-site. Not all vacuums are created equal. The most important feature of a commercial-rated vacuum is the size of the particle it will capture. The type of filter that is rated to capture ultra-fine dust is a HEPA (high-efficiency particulate Air filter). A HEPA is the last filter in the defense of cleaning the air. There are 2 to 3 main filters that will do the majority of the work.
When the vacuum is full, it needs to be emptied. This is the tricky part. The vacs bought at a home store, when emptied, will allow dust back into the air. A commercial extractor will have a continuous discharge bag system ending this situation. This allows all dust from the extractor to be disposed of properly and legally.
If the floor is cracked or has open floor joints, these will need to be filled. The first step will be to clean the void from the impacted debris and widen it a bit. A walk-behind joint saw can be used to perform the work. Once all the voids are clean, they can be filled with joint-filling material, keeping them clean.
Depending on what type of flooring will be installed, the surface might need to be prepared more than just sweeping. A shot blaster or grinder can be used to not only provide the proper surface profile, but it can also remove any bacteria at the near-surface. Both are connected to a commercial vacuum fitted with a HEPA filter capturing the contaminated debris.
Benefits of Professional Surface Restoration for Disaster Recovery
There will be times when a professional disaster recovery team will need to be called. After reviewing the information above, you might feel it is too much to manage depending on your experience level. Professionals will know when harmful microbe treatment will be needed. They also have an understanding of when a structural engineer should be called. Safety should be the first concern before stepping into a disaster zone.
Conclusion
No one ever wants to be in a natural disaster. If you are in a geographical area that is prone to have them, preparation is important. Having a disaster plan set forth with your family or employees is the first step. Knowing where to go and what needs to be done could save lives.
With equipment, seldom will you have everything needed to restore a structure to its original condition. DiamaPro Systems has almost everything needed. Auto-scrubbers, dust extractors, air scrubbers, and scrapers are all available. Call us for help when choosing the equipment!