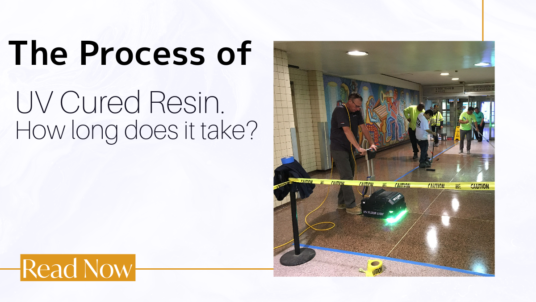
Resinous flooring has been around for over one hundred years worldwide and was introduced into the U.S. in the early 1960’s. Most resins up to that point have been two-part materials, a resin and a catalyst. When combining the two components a chemical reaction occurs to produce a “cured” film. This film will have various levels of performance depending on what they have been formulated to do. Whether it be to protect from chemical attack, increase the abrasion resistance, or add color, the developer (chemist) can tweak the formula to meet the intended needs. This is why resinous flooring systems are currently so popular today.
About the same time resinous flooring was introduced to the U.S., chemists were working on using ultra-violet light to cure adhesives. This curing process would speed up production lines enabling higher level of goods produced. Once they perfected the use of photo-initiators in the adhesives they incorporated the technology into flooring resins. Hence, UV Cured Resins for concrete.
There are different formulations of UV Cured Resins for concrete, but they all have several things in common, they have a photo-initiator and resin, they use a level of ultraviolet light for curing, and they protect concrete. The most durable and widely used for concrete is the high solids formulation such as DiamaPro® UV-HS Plus.
Curing is performed using a high-intensity ultraviolet light while the material is in a wet state. Once applied, a UV light is rolled over the wet material. You have wet material in front of the light and cured material behind the curing lamp in the light. The wheels of the light are rolling on cured material as you move across the floor leaving no wheel marks in the coating. This is all done with the reaction between the photo-initiator in the material and high-intensity ultraviolet light.
There are advantages to the UV curing process. The most obvious is speed. Once the curing light rolls over the material, the floor can be put into service reducing the normal downtime that occurs when using a chemical-cured material. This could be 8-10 hours too many days depending on the chemical-cured material used.
UV curing is very efficient and uniform. The single-part material needs no mixing to produce a durable film. Chemical-cured materials require the exact ratio of each part then completely mixed for a predetermined amount of time with the proper mixing paddle at an rpm decided by the manufacturer. If not performed correctly, the durability of the final film will be compromised.
UV cured materials and chemical cured materials both go through a cross-linking process to develop a film. The cross-linking process is much more efficient with the UV cured material. This develops a more durable film even if the resins are similar in each. This efficient cross-linking is shown with the DiamaPro® UV-HS Plus UV cured material by the independent 14-day Skydrol LD-4 chemical resistance test. Skydrol LD-4 is the most aggressive hydraulic fluid that you can find in the aviation industry. The results showed no effect on the coating or substrate after the 14-day independent lab test.
Some of the current UV cured formulations, such as DiamaPro® UV-HS Plus, are infused with Microban® Technologies. These technologies have anti-microbial properties to reduce the growth of harmful microbes and are registered with the EPA. This is an especially important feature when protecting a surface that will be in contact with microbe growing debris such as solid food, grease, and many liquids.
The maintenance of a UV Cured System is amazingly simple. Select the cleaning solution that will remove the contamination. There is no cleaning chemical solution that is typically used that will have an impact on the cured material. If the system starts to wear, it can be recoated with a light screening and solvent wipe for surface preparation. Apply another single coat and it will look like new.
When evaluating UV Cured Resins for concrete look at:
- The length of time the system has been on the market.
- If there is a chemical-resistant chart.
- Application procedures.
- The brand of curing light recommended.
- The speed the light should travel to obtain a full cure.
- How the cured system is to be cleaned.
- The re-coat processes.
If you have any questions regarding UV-cured resin coatings or would like more information DiamaPro UV-HS Plus, visit our contact page and fill out the form or give us a call at 470-977-2323 and we can help find a certified contractor near you!