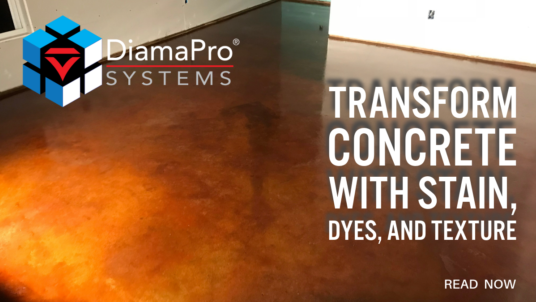
A concrete surface can be manipulated producing a multitude of textures. These textures, such as sandblasted or broomed, will reflect light differently depending on the aggressiveness and the direction they are running. The amount and how the light reflex, will produce different shades. These shades can be used as a color.
Scoring is also a technique that can add dimension or separation. A score line is a shallow, uniform impression on the surface of the concrete floor made by a saw fitted with a diamond blade. You can separate colors by making a ¼’ deep score line. Once the slab is colored, a score will appear as a grout joint. The score will remove the color and uncover the natural concrete color. Scores can be used to conceal control joints by using the control joint as part of the score design.
If natural concrete lacks color, dyes, and stains can be added. These materials are topically applied, and all require a level of surface preparation to perform. They have their unique ways of developing color. Stains might penetrate to impart color, but others lay on the surface, and the rest react with the concrete to produce color.
Types of Concrete Stain
Dyes and stains are different, but the terms are used synonymously. Dyes, such as DiamaPro® Diama-Color, are colored solutions that penetrate the concrete surface. Once a dye particle is in solution, it cannot be strained from the liquid. Once the carrier (liquid material) evaporates, the dye becomes a particle imparting color. They can color a rough or smooth surface. Dyes are usually translucent showing concrete. They will not hide imperfections, only add color to what they have penetrated.
Non-reactive stains like DiamaPro® Diama-TLC are made up of a carrier, which could be water or solvent, and pigment in suspension. Suspension is when the pigmented particle is floating in a carrier. They tend to settle in the container. If the manufacturer recommends mixing before use, it is likely in suspension. There could also be a binder included. The binder is to bond the pigment particle to the substrate. Binders include acrylic, epoxy, urethane, and silicate. They are all different chemistries but all bond pigment to concrete. These types of stains are more film-forming than penetrating.
Reactive stains develop color by chemically reacting with the concrete substrate. Acid stains have been around since the early 1920’s. They do not hold any colored particles that provide color. They have chemicals that react with a part in concrete, calcium hydroxide, producing color. The color of the liquid has no impact on the final color it produces.
The amount and intensity of color chemical reactive stains develop depends on many factors. The liquid acid stain by itself will not develop color. It needs to have a substrate that has calcium hydroxide. Chemical reactions can be affected by the environment. Applying an acid stain at 50-degree temperatures will produce a lighter color than applying it at 80 degrees on the same substrate. The color produced will be very inconsistent in an effective way. That is the attraction to acid stains. No two floors will look alike.
Where Stain Shines
Stains are great at adding color to a boring concrete slab. It could be a decorative border, an accent in the main field, or the entire area. Some stains can be used interior and exterior. Usually, chemical reactive and non-reactive stains are best for exterior projects. When using any coloring method exterior, it must be UV stable. The ultraviolet light from the sun can have an adverse effect on non-stable pigments. It can lighten or even change their color.
Stains can be successfully applied to a broom-finished, imprinted, flat troweled, or polished concrete but the right stain needs to be selected. All these scenarios have a different absorption rate. Selecting a stain type for the surface and environment it will be in is important.
Sealer and Protective Coatings
Stains and dyes are coloring methods. They offer little to no protection value for the concrete substrate. Abrasion, chemical resistance, and cleanability are all things that should be considered during the selection process. There are sealers and protective coatings that can be applied to a stained or dyed floor. Epoxies, urethanes, polyaspartic, and acrylics have all been used in a clear form.
Sealers will have an impact on the final color. When applying a film-forming material that has good penetration, it will darken the floor. This darkening effect will deepen and enhance the color. It produces a rich, warm appearance.
The performance of the sealer is related to the performance needed for the environment you are in. Will it have spilled chemicals, forklift traffic, grease, foodstuff or is it interior or exterior? Select a sealer that fits the needs of the facility.
Facility Types
Stains and dyes can be installed in almost any facility. Churches, schools, office buildings, restaurants, and residential homes are prime candidates. Industrial facilities use stains to incorporate safety lines onto their floors. When you want color, this is a straightforward way to obtain it. The color choice is great. When using a pigmented stain, most wall paint suppliers can provide you with almost every color under the rainbow.
Conclusion
Once you have a good understanding of the correct surface preparation, application techniques, and where it should be used, the rest is practice. Looking at images of stained concrete on the internet is really a testament to the installer. Quality stain installers are artists. They manipulate the available coloring methods in a way that suits their project.
Stain and dye manufacturers and suppliers will train the proper installation techniques. DiamaPro Systems has concrete stains and dyes for any application. We have trained field personnel that can help you start in the right direction. Once the basics are in place, the fun stuff can begin. A project can incorporate one or multiple colors and methods. It goes back to basics. Once they are in place, your creativity can begin.